Чёрная металлургия
Чёрная металлургия — отрасль тяжёлой промышленности, объединяющая технологически и организационно предприятия по добыче и обогащению рудного и нерудного сырья, по производству огнеупоров, продуктов коксохимической промышленности, чугуна, стали, проката, ферросплавов, стальных и чугунных труб, а также изделий дальнейшего передела (рельсовых скреплений, белой жести, оцинкованного железа), металлических порошков чёрных металлов[1]. Основным исходным сырьём для получения чёрных металлов являются железная руда, коксующиеся угли и руды легирующих металлов.
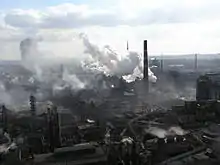
История
Добыча железа началась, по крайней мере, за два тысячелетия до нашей эры. Получение чистого железа, его сплавов стало возможным благодаря опыту, накопленному древними металлургами по выплавке меди и её сплавов с оловом, серебром, свинцом и другими легкоплавкими металлами.
Плавку железа в древности производили в ямах-горнах, обмазанных глиной или выложенных камнем. В горн загружали дрова и древесный уголь. Через отверстие в нижней части горна нагнетали с помощью кожаных мехов воздух. На смесь древесного угля и дров засыпали измельчённую железную руду. Сгорание дров и угля проходило интенсивно. Внутри горна достигалась относительно высокая температура[2].
Благодаря взаимодействию угля и оксида углерода СО, образовавшегося при сгорании угля, с оксидами железа, содержавшимися в руде, железо восстанавливалось и в виде тестообразных кусков накапливалось на дне горна. Куски были загрязнены золой, шлаком, выплавлявшимся из составляющих руды. Такое железо называли сыродутным. Из него необходимо было удалить примеси прежде, чем приступить к изготовлению изделий. Разогретый металл ковали и на наковальне выжимали остатки шлака, примесей и др. Отдельные куски железа сваривали в единое целое. Такой способ существовал вплоть до XII—XIII веков.
Когда стали использовать энергию падающей воды и приводить в движение меха механическим способом, удалось увеличить объём воздуха, подаваемого в горн. Горн сделали больше, стенки его выросли из земли, он стал прообразом доменной печи — домницей. Домницы имели высоту в несколько метров и сужались кверху. Сначала они были квадратными, потом стали круглыми. Подачу воздуха производили через несколько фурм. В нижней части домницы имелось отверстие, замазываемое глиной, через которое после окончания плавки вынимали готовое железо. Улучшение технологии плавки, обкладки стенок домницы природным огнеупорным камнем позволили значительно повысить температуру в горне. На дне печи образовывался жидкий сплав железа с углеродом — чугун. Вначале чугун считали отходом производства, так как он был хрупким (отсюда появилось английское название чугуна — pig iron, свиное железо). Позже заметили, что чугун обладает хорошими литейными свойствами и из него стали отливать пушки, ядра, архитектурные украшения[3].
В начале XIV в. из чугуна научились приготовлять ковкое железо, появился двухступенчатый способ производства металла. Куски чугуна переплавляли в небольших тиглях — горнах, в которых удавалось получать высокую температуру и создавать окислительные условия в области фурм. Благодаря окислению из чугуна выжигали большую часть углерода, марганца, кремния. На дне тигля собирался слой железной массы — крица. Масса была загрязнена остатками шлака. Её извлекали из тигля клещами или ломом и тут же в разогретом состоянии подвергали ковке для выдавливания загрязнений и сваривания в один прочный кусок. Такие горны назывались кричными. Они обладали большей производительностью, чем сыродутные, и давали металл более высокого качества. Поэтому со временем получение сыродутного железа было прекращено. Выгоднее было получать железо из чугуна, чем непосредственно из руды. По мере улучшения качества железа возрастали и потребности в нём в сельском хозяйстве, военном деле, строительстве, промышленности. Возрастало производство чугуна, домницы увеличивались в размерах, постепенно превращаясь в доменные печи. В XIV веке высота доменных печей достигала уже 8 метров.
Ускоренное развитие металлургии началось после замены древесного угля коксом. Вырубка лесов для получения древесного угля привела к тому, что уже в XV веке в Англии было запрещено использовать древесный уголь в металлургии. Применение кокса не только удачно решило проблему топлива, но и благоприятствовало росту производительности доменных печей. Благодаря повышенной прочности и хорошей теплотворной способности кокса стало возможным увеличение диаметра и высоты печей. Позднее были успешно проведены опыты по использованию доменного колошникового газа для подогрева дутья. Раньше все газы выбрасывались в атмосферу, теперь колошник стали делать закрытым и улавливали отходящие газы.
Одновременно совершенствовался и способ получения стали. Кричный способ уже не мог удовлетворить потребности в железе. Прочность сталям придавал углерод. Науглероживание кричного железа производили либо в твёрдом состоянии, либо сплавлением с чугуном в маленьких тиглях. Но такие методы не могли дать много стали. В конце XVIII века на металлургических заводах появился новый процесс — пудлингование. Сущность процесса пудлингования заключалась в том, что топка была отделена от ванны, в которой расплавляют чугун. По мере окисления примесей из жидкого чугуна выпадали кристаллы твёрдого железа, которые накапливались на поду ванны. Ванну перемешивали ломом, намораживали на него тестообразную железную массу (до 50 кг) и вытаскивали из печи. Эту массу — крицу обжимали под молотом и получали железо.
В 1856 году Генри Бессемер в Англии разработал наиболее производительный способ получения стали из чугуна — продувкой воздухом жидкого чугуна в конвертере, выложенном изнутри кремнезёмистым кирпичом. В бессемеровских конвертерах перерабатывали чугуны с повышенным содержанием кремния. Процесс шёл быстро: 15-18 т чугуна превращались в сталь в течение 15-20 мин. Для переработки чугуна с повышенным содержанием фосфора Томасом был предложен конвертер с футеровкой из оксидов кальция и магния[4].
В 1864 году в Европе появились первые мартеновские печи, в которых расплавление чугуна, окисление его примесей производили в подовых (отражательных) печах. Печи работали на жидком и газообразном топливе. Газ и воздух подогревали теплом отходящих газов. Благодаря этому в печи развивались настолько высокие температуры, что стало возможным на поду ванны иметь не только жидкий чугун, но и поддерживать в жидком состоянии более тугоплавкое железо и его сплавы. В мартеновских печах начали получать из чугуна сталь любого состава и использовать для переплава стальной и чугунный лом. В начале XX века появились электрические дуговые и индукционные печи. В этих печах выплавляли легированные высококачественные стали и ферросплавы. В 50-х годах XX века начали использовать процесс передела чугуна в сталь в кислородном конвертере продувкой чугуна кислородом через фурму сверху. Сегодня это наиболее производительный метод получения стали. В последние годы появились значительно усовершенствованные по сравнению с прошлым процессы прямого получения железа из руды.
Развитие сталеплавильного производства повлекло за собой и развитие нового оборудования для горячей и холодней обработки стали. В конце XVIII века появились прокатные станы для обжатия слитков и проката готовых изделий. В первой половине XIX века начали применять крупные паровые и воздушные молоты для ковки тяжёлых слитков. Последняя четверть XIX века ознаменовалась появлением крупных прокатных станов и станов для непрерывной прокатки с электрическими приводами.
История развития чёрной металлургии в России
В России до XVII в. производство железа носило кустарный характер. Выплавкой железа занимались отдельные крестьянские семьи или совместно несколько крестьянских дворов. Строили домницы на землях Новгородчины, Псковщины, в Карелии. В начале XVII в. появились доменные печи на Городищенских заводах около Тулы, началось строительство заводов на Урале. В 1699 году был построен Невьянский завод. Бурное производство чугуна началось при Петре I. Демидовыми на Урале была построена колоссальная по тем временам печь высотой в 13 м, выплавлявшая в сутки 14 т чугуна. Большие земельные вотчины, лежащие рядом с заводом, приписывались к заводу вместе с крестьянами, которые обязаны были отрабатывать на нём определённое время. Крепостное право в течение длительного времени обеспечивало заводы рабочей силой. Хорошие природные условия — руда, лес, из которого выжигали уголь, обилие воды, энергию которой использовали для приведения в движение различных механизмов, — способствовали бурному развитию русской металлургии. Чугун начали экспортировать за границу[5].
Но в XIX веке крепостное право стало тормозом в развитии производства. Страны Европы и США обогнали Россию по производству чугуна и стали. Если с 1800 по 1860 год производство чугуна в России увеличилось только в два раза, то в Англии оно возросло в десять раз, во Франции — в восемь раз. Владельцы русских заводов, имевшие в своём распоряжении дешёвую рабочую силу, не заботились о развитии производства, о внедрении технических новшеств, облегчении условий труда рабочих. Постепенно старые уральские заводы приходили в упадок и останавливались.
Министерство финансов, в ведении которого находилась горно-металлургическая отрасль, стремилось внедрять в стране передовые технические достижения, в первую очередь британские. Отчёты о достижениях европейской промышленности, составляемые зарубежными «агентами» Корпуса Горных Инженеров, регулярно печатались на страницах «Горного журнала». Так, например, об изобретении Нилсоном нагрева доменного дутья и многих других, российские металлурги и промышленники узнавали уже через несколько месяцев после их оглашения. Например, ещё в 1830-х годах, вскоре после того, как Дж. Нилсон внедрил своё изобретение, Христофор Иоакимович Лазарев, представитель знаменитого армянского рода промышленников и меценатов, провёл на Чёрмозском заводе в Пермском крае успешные опыты по использованию нагретого дутья. Но даже готовые технические решения практически не были востребованы, поскольку внешний спрос на русское железо иссяк ещё в начале века, после того, как Великобритания стала сама обеспечивать себя металлом, а внутренний спрос был крайне низок. Количество инициативных, предприимчивых людей, способных и желающих внедрять инновации, было невелико, поскольку бо́льшая часть населения страны не имела никаких прав, не говоря уже о капиталах. В результате даже те инновации, которые внедрялись наиболее технически грамотными и предприимчивыми заводовладельцами, представляли собой скорее дань технической моде, нежели реальный инструмент повышения экономической эффективности[6].
Ситуация изменилась в конце XIX в. — наметился подъём в чёрной металлургии России, особенно в южных районах (Украина). В 1870 г. русский купец Пастухов построил в Сулине завод для выплавки чугуна на донецком антраците. В местечке Юзовка (ныне Донецк) был пущен крупнейший по тому времени Юзовский металлургический завод. Бурное развитие металлургия Юга получила с открытием залежей железных руд Кривого Рога. В сочетании с запасами донецких углей это стало основой развития горнорудной промышленности Юга России. В отличие от заводов Урала южные заводы были оборудованы более крупными агрегатами. В доменные печи загружали кокс и выдавали в сутки примерно в шесть-семь раз больше чугуна, чем в печах, работающих на древесном угле.
В 1870 году на Сормовском заводе в Нижнем Новгороде заработали первые мартеновские печи, а в Донбассе в сталелитейных цехах появились и конвертеры. В 1910 году была установлена первая дуговая сталеплавильная печь, а в конце 1917 году под Москвой стал работать электрометаллургический завод с несколькими электропечами[5].
В годы гражданской войны развитие металлургии было приостановлено, и только в 1926 г. был достигнут уровень 1913 году — максимальной дореволюционной выплавки стали в 4,3 млн т. Интенсивное развитие чёрная металлургия в СССР получила в годы первых пятилеток. Были построены крупнейшие в мире комбинаты — Магнитогорский и Кузнецкий; заводы Запорожский, «Азовсталь», Криворожский. Подвергались коренной реконструкции старые заводы: Днепропетровский, Макеевский, Нижне-Днепровский, Таганрогский. Построены новые заводы высококачественных сталей: «Электросталь», «Днепроспецсталь». В 1940 году производство стали достигло 18,5 млн т и проката 13,1 млн т.
Великая Отечественная война нанесла серьёзный урон южным заводам СССР. Большая часть оборудования металлургических заводов была эвакуирована на Восток. В кратчайшие сроки на Урале и в Сибири было развёрнуто производство металла, необходимого для победы. Построены новые заводы — такие, как Челябинский, расширено производство на Кузнецком и Магнитогорском металлургических комбинатах, вывезенное оборудование устанавливалось на заводах в Златоусте, Нижнем Тагиле, Серове. Были освоены новые марки броневой, орудийной стали, налажен выпуск необходимых сортов проката. Металлурги страны создали в короткие сроки базу для наращивания всех видов вооружений и уже в 1943 г Советский Союз значительно превосходил врага по производству танков, орудий, самолётов и другой техники. В послевоенные годы чёрная металлургия быстро оправилась от потерь. К 1950 г. уровень выплавки чёрного металла в полтора раза превысил довоенный. Все последующие пятилетки характеризуются последовательным наращиванием объёмов производства, строительством новых заводов и цехов. Крупнейшими стали комбинаты: Магнитогорский, Новолипецкий, Западно-Сибирский, Криворожский, Череповецкий, Челябинский и ряд других. Появились кислородные конвертеры ёмкостью до 350 т, 900 т мартеновские печи, двухванные сталеплавильные агрегаты, 200-т дуговые электропечи, доменные печи с полезным объёмом 5000 м3. Построены непрерывные станы для получения листа, сортового проката, труб, установки для непрерывной разливки стали (УНPC). Получила развитие специальная металлургия высококачественных сталей и сплавов: процессы получения стали на установках электрошлакового, вакуумного индукционного, вакуумно-дугового, электронно-лучевого, плазменно-дугового переплавов.
Широко применяются такие методы, как обработка жидкой стали в ковше синтетическим шлаком и аргоном, вакуумирование жидкого металла. В 1974 году по объёму производства чёрных металлов СССР вышел на первое место в мире. В годы XI пятилетки на техническое перевооружение отрасли было затрачено около 6 млрд руб. Были построены конвертеры вместимостью 350 т. электропечи с мощностью трансформатора 60—80 МВА, мощность установок по непрерывной разливке стали достигла 20 млн т в год. Построены новые коксовые батареи, агломерационные фабрики, горнообогатительные комбинаты, в том числе Костомукшский ГОК, вошёл в строй Оскольский электрометаллургический комбинат по производству стали из железа прямого восстановления, начали работать два электрометаллургических завода в Белоруссии и Молдавии производительностью по 600 тыс. т готового проката в год. Продолжается выведение из эксплуатации старых агрегатов, работа которых экономически нецелесообразна. Значительное внимание уделяется повышению качества металла на всех стадиях его производства. Проведены большие работы по улучшению качества подготовки железорудного сырья.
На рубеже 1990—2000-х годов произошло резкое увеличение производства стали в конвертерных цехах и закрытие мартеновских цехов на металлургических комбинатах.
Вклад российских и советских учёных
Большую роль в развитии отечественной металлургии сыграли выдающиеся учёные[7].
- П. П. Аносов разработал основы теории производства литой высококачественной стали.
- Д. К. Чернов является основоположником научного металловедения, его труды по кристаллизации стали не потеряли своего значения и в настоящее время.
- Академики А. А. Байков, М. А. Павлов, Н. С. Курнаков создали глубокие теоретические разработки в области восстановления металлов, доменного производства, физико-химического анализа.
- В. Е. Грум-Гржимайло, А. М. Самарин, М. М. Карнаухов заложили основы современного сталеплавильного и электросталеплавильного производства.
- Академик И. П. Бардин известен во всем мире своими трудами в области доменного производства и организацией научных металлургических исследований.
Состав
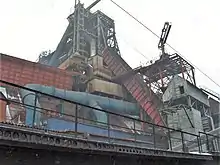
В состав чёрной металлургии входят следующие основные подотрасли:
- добыча и обогащение руд чёрных металлов (железная, хромовая и марганцевая руда);
- добыча и обогащение нерудного сырья для чёрной металлургии (флюсовых известняков, огнеупорных глин и т. п.);
- подготовка сырья к доменной плавке (окускование);
- производство чёрных металлов (чугуна, углеродистой стали, проката, металлических порошков чёрных металлов);
- производство стальных и чугунных труб;
- коксохимическая промышленность (производство кокса, коксового газа и пр.);
- вторичная обработка чёрных металлов (разделка лома и отходов чёрных металлов).
Металлургический цикл
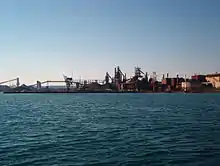
Собственно металлургическим циклом является:
- чугунно-доменное производство;
- производство стали (мартеновское, кислородноконвертерное и электросталеплавильное) + непрерывная разливка;
- производство проката (прокатное производство).
- иногда добавляют четвёртый предел : производство труб, автомобильных листов.
Предприятия, выпускающие чугун, углеродистую сталь и прокат, относятся к металлургическим предприятиям полного цикла. Предприятия без выплавки чугуна относят к так называемой передельной металлургии. «Малая металлургия» представляет собой выпуск стали и проката на машиностроительных заводах. Основным типом предприятий чёрной металлургии являются комбинаты. В размещении чёрной металлургии полного цикла большую роль играет сырьё и топливо, особенно велика роль сочетаний железных руд и коксующихся углей. С середины XX века в металлургии начинает применяться прямое восстановление железа.
Все металлургические переделы являются источниками загрязнения пылью, оксидами углерода и серы[8]
Чёрная металлургия в XXI веке
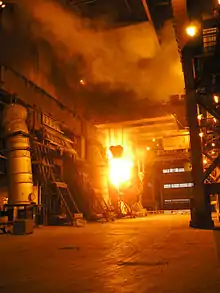
По данным на 2007 год, на страны Азии (без стран СНГ) приходилось 59 % мирового выпуска стали. При этом 36 % мировой выплавки стали приходилось на КНР (больше, чем на Северную Америку, Европу и Японию, вместе взятые)[9]. Интенсивный рост чёрной металлургии в Китае в начале ХХI века вызвал появление десятков новых крупных центров выплавки стали мирового значения. В частности, гигантский узел чёрной металлургии сложился вокруг Таншаня[10]. В одной провинции Хэбэй выплавляется больше стали, чем в США[11]. Япония занимала второе после Китая место по производству стали (9 %). Практически весь остальной выпуск стали в Восточной Азии приходился на Южную Корею и Тайвань[9]. Крупнейшим сталеплавильным предприятием в мире и самым большим заводом с доменным металлургическим циклом является металлургический комбинат компании «POSCO» в южнокорейском городе Кванъян[11]. На прочие регионы Азии приходилось 8,5 % мировой выплавки стали[9].
На страны Европы и СНГ в 2007 году приходилось 25 % мирового производства стали.
На США и Канаду в 2007 году приходилось 8,5 % мирового выпуска стали, из них 7,5 % приходилось на США. На Латинскую Америку приходилось 5 % производства стали в мире.
Доля Африки в мировом производстве стали составляла в 2007 году менее 1,5 %, Австралии и Новой Зеландии — 1 %.
Доля комбинатов полного цикла в мировой выплавке стали в 2007 году составляла 70 %. Около 97 % выплавки стали из чугуна производилось кислородно-конверторным способом. Мартеновские печи продолжали использовать только на Украине, в России, Индии, Узбекистане и Латвии.
Крупнейший в мире район производства стали из лома существует на юге США. На базе металлолома существует чёрная металлургия многих европейских государств, некоторых стран Центральной и Южной Америки, Юго-Западной Азии и Северной Африки, а также стран Африки южней Сахары (кроме ЮАР и Зимбабве).
Около 15 % мировой выплавки стали в электропечах в 2007 году было основано на технологии прямого восстановления железа. Оно было сосредоточено в основном, в Латинской Америке, Южной Азии, Юго-Западной Азии и Северной Африке. В Латинской Америке 98 % выпуска продуктов прямого восстановления железа осуществлялось в четырёх странах (Венесуэла, Мексика, Тринидад и Тобаго, Аргентина) с использованием местного природного газа. Все производство этих продуктов в Юго-Западной Азии и Северной Африке также было основано на восстановлении железа природным газом и было сосредоточено в пяти странах (Иран, Саудовская Аравия, Катар, Египет, Ливия). На Индию приходилось 28 % мирового выпуска продуктов прямого восстановления железа), в основном, в результате восстановления металла из руды некоксующимися марками угля[9].
Основными мировыми транснациональными компаниями чёрной металлургии являются Arcelor Mittal, Tata Steel, Gerdau, U.S. Steel, «Северсталь», «Евраз», Techint[10].
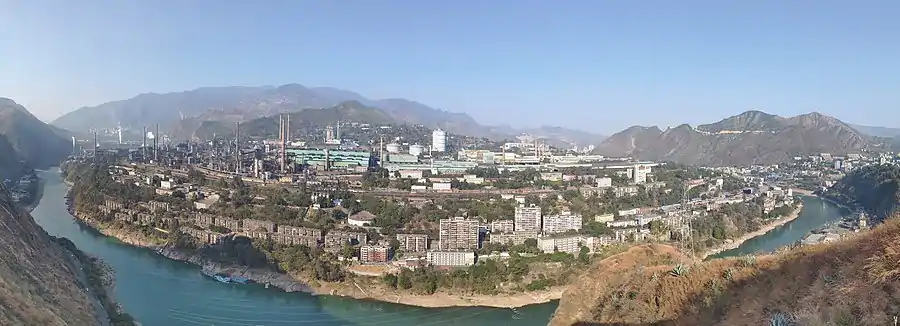
В России
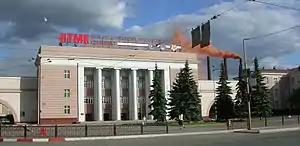
Особенность промышленности России заключается в больших расстояниях между производствами различных циклов. Металлургические комбинаты, производящие чугун и сталь из руды, традиционно располагались около месторождений железных руд в районах, богатых лесом, так как для восстановления железа использовали древесный уголь. И в настоящее время металлургические комбинаты металлургической отрасли России расположены вблизи месторождений железной руды: Новолипецкий и Оскольский — около месторождений центральной России, Череповецкий («Северсталь») — около Карельского и Костомукшского, Магнитогорский — около горы Магнитная (уже выработанное месторождение) и в 300 км от Соколовско-Сарбайского в Казахстане, бывший Орско-Халиловский комбинат (в настоящее время «Уральская сталь») около месторождений природнолегированных руд, Нижнетагильский — вблизи Качканарского ГОКа, Новокузнецкий и Западно-Сибирский — около месторождений Кузбасса. Все комбинаты России расположены в местах, где ещё в XVIII веке и ранее существовало производство железа и изделий из него с использованием древесного угля. Месторождения коксующегося угля расположены чаще всего вдали от комбинатов именно по этой причине. Только Новокузнецкий и Западно-Сибирский металлургические комбинаты расположены непосредственно на месторождениях каменного угля Кузбасса. Череповецкий металлургический комбинат снабжается углём, добываемом в Печорском угольном бассейне.
В центральной части России большая часть железорудного сырья добывается в районе Курской аномалии. В промышленных масштабах железорудное сырьё производится также в Карелии и на Урале, а также в Сибири (добыча ведётся в Кузбассе, Красноярском крае, Хакасии и близких им районах). Большие запасы железной руды в Восточной Сибири практически не осваиваются из-за отсутствия инфраструктуры (железных дорог для вывоза сырья).
Два основных района производства коксующегося угля в России — Печорский и Кузнецкий угольные бассейны. Крупные угольные поля есть также в Восточной Сибири; они отчасти разрабатываются, однако промышленное их освоение упирается в отсутствие транспортной инфраструктуры.
Центральная часть России, в частности Воронеж, Тула не богаты металлами, поэтому в основном для внутренних нужд все сырьё привозится из других регионов. Крупнейшими поставщиками металла в центральный регион являются общероссийские компании, такие как ЕВРАЗ Металл Инпром, и местные, такие как ПРОТЭК и Союзметаллкомплект.
При строительстве всех крупных металлургических комбинатов России (в советское время) одновременно велось и строительство ориентированного на каждый завод горно-обогатительного комбината. Однако, после распада СССР, некоторые комплексы оказались разбросанными по территории СНГ. Например, Соколовско-Сарбайское ГПО, поставщик руды на Магнитогорский меткомбинат, теперь находится в Казахстане. Железорудные предприятия Сибири ориентированы на Западно-Сибирский и Новокузнецкий меткомбинаты. Качканарский ГОК поставляет руду на Нижнетагильский меткомбинат. Костомукшский ГОК поставляет руду в основном на Череповецкий металлургический комбинат.
При размещении предприятий учитывалось также обеспечение водой, электроэнергией, природным газом.
В России созданы три металлургические базы:
- Уральская металлургическая база
- Центральная металлургическая база
- Сибирская металлургическая база
Примечания
- Чёрная металлургия . Дата обращения: 28 марта 2015. Архивировано 5 июля 2015 года.
- Линчевский, 1986, с. 8.
- Линчевский, 1986, с. 9.
- Линчевский, 1986, с. 10.
- Линчевский, 1986, с. 11.
- Карабасов, 2014, с. 95.
- Линчевский, 1986, с. 12.
- Н. П. Большина. Экология металлургического производства . Дата обращения: 26 марта 2018. Архивировано 26 марта 2018 года.
- Черная металлургия мира: современное размещение. Ч.1 . Дата обращения: 20 августа 2021. Архивировано 20 августа 2021 года.
- Черная металлургия мира: современное размещение. Ч.2 . Дата обращения: 20 августа 2021. Архивировано 20 августа 2021 года.
- Металлургические мировые рекорды . Дата обращения: 20 августа 2021. Архивировано 20 августа 2021 года.
Литература
- Линчевский Б. В., Соболевский А. Л., Кальменев А. А. Металлургия чёрных металлов: Учебник для техникумов — 2-е издание, перераб. и дополн. — Металлургия, 1986. — 360 с. — 12700 экз.
- Татарченко Д. М. Металлургия чугуна, железа и стали в общедоступном изложении. — 3-е. — ГТТИ, 1932. — 492 с.
- Юсфин Ю. С., Пашков Н. Ф. Металлургия железа: Учебник для вузов. — Москва: Академкнига, 2007. — 464 с. — ISBN 978-5-94628-246-8.
- Карабасов Ю. С., Черноусов П. И., Коротченко Н. А., Голубев О. В. Металлургия и время : Энциклопедия : в 6 т. — М. : Издательский Дом МИСиС, 2014. — Т. 6 : Металлургия и социум. Взаимное влияние и развитие. — 224 с. — 1000 экз. — ISBN 978-5-87623-760-6 (т. 6).
Ссылки
- «Чёрные металлы» — производственный журнал по вопросам чёрной металлургии Архивная копия от 24 марта 2016 на Wayback Machine (rudmet.ru)
- Металлургические мировые рекорды Архивная копия от 20 августа 2021 на Wayback Machine