Агломерация (металлургия)
Агломера́ция (от лат. agglomero — присоединяю, накопляю) — метод термического окускования пылеватых мелких руд, концентратов и металлосодержащих отходов путём их спекания. Наиболее широко агломерация применяется для подготовки железорудного сырья для металлургического производства чугуна[1][2]. Процессы, происходящие в спекаемом слое шихты при агломерации, во многом схожи с процессами спекания частиц при производстве керамики и в процессах порошковой металлургии[3].
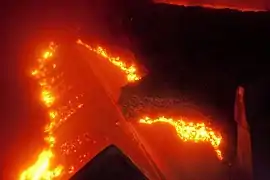
Агломерацию применяют при обжиге железных руд, и концентратов, а также руд и концентратов цветных металлов[4]. Железорудный агломерат наряду с окатышами используется в производстве чугуна в качестве основного сырья[5].
История
_(14594947629).jpg.webp)
Агломерация как способ окускования был открыт случайно в 1887 году английскими исследователями Ф. Геберлейном и Т. Хатингтоном в ходе опытов по десульфурирующему обжигу руд цветных металлов на колосниковой решетке[6]. Обжиг проводили следующим образом. На колосниковую решетку насыпали слой горящих кусков кокса или угля, на который затем укладывали слой сульфидной руды. Снизу через решетку подавали воздух от воздуходувки. Проходя через слой топлива, воздух обеспечивал его интенсивное горение. Горячие продукты горения, двигаясь дальше, нагревали расположенный выше слой руды. При температурах 400—500 °С происходило воспламенение сульфидов. В результате их горения выделялось дополнительное тепло, которое потоком газа переносилось в слой руды, расположенный еще выше. Таким образом, зона горения сульфидов перемещалась в направлении движения газа, проходя последовательно весь слой руды, расположенный на решетке. Обжиг руды осуществлялся без подвода тепла извне—только за счет тепла, выделявшегося при горении сульфидов. «Запальное» топливо (куски раскаленного кокса или угля), расположенное вначале на колосниковой решетке, служило только для воспламенения сульфидов руды самого нижнего слоя[7].
В ходе исследований выяснилось, что при обжиге руд с высоким содержанием серы выделялось так много тепла и температура поднималась до такого уровня, что происходило приплавление обожженных кусков руды друг к другу. После окончания процесса слой руды превращался в закристаллизовавшуюся пористую массу — спёк. Куски раздробленного спёка, которые назвали «агломерат», оказались вполне пригодными по своим физико-химическим свойствам для шахтной плавки[7].
Сравнительная простота технологии и высокая тепловая эффективность слоевого окислительного обжига сульфидных руд привлекли внимание специалистов черной металлургии. Появилась идея разработать термический способ окускования железорудных материалов на базе подобной технологии. Отсутствие в железных рудах серы как источника тепла предполагалось компенсировать добавкой к руде мелких частиц углеродистого топлива: угля или кокса. Железорудный агломерат по такой технологии в лаборатории впервые был получен в Германии в 1902—1905 гг.[8]
Первой промышленной установкой для производства агломерата был котел Геберлейна — коническая стальная чаша, на некотором расстоянии от днища которой была закреплена колосниковая решётка, а в днище имелся патрубок для подвода дутья от воздуходувки. Процесс отличался тем, что источником тепла для размягчения и частичного плавления рудных зёрен были горящие частички угля или кокса. На находящийся на колосниковой решётке слой из кусков раскаленного твердого топлива засыпали тонким слоем агломерационную шихту — смесь мелкой влажной руды с частичками кокса. После этого включали дутьё, и подогретый в слое горящего на колосниковой решетке топлива газ поднимался вверх, воспламеняя и сжигая содержащееся в шихте топливо в нижнем слое спекаемого материала. Когда зона горения доходила до поверхности, загружался следующий слой агломерационной шихты. Таким образом процесс продолжался до тех пор, пока вся чаша не заполнялась готовым агломератом (котел емкостью 15 т заполнялся в течение 12 часов). После этого выключали вентилятор, опрокидывали котёл и вручную разбивали полученную глыбу агломерата на более мелкие куски[9].
В России первые 6 котлов Геберлейна были введены в эксплуатацию в 1906 г. на Таганрогском заводе, а в 1914 г. — ещё 5 чаш на Днепровском металлургическом заводе. Одновременно в эти же годы велись работы по созданию альтернативных аглоустановок, лишённых недостатков котлов Геберлейна: низкой производительности, тяжёлого физического труда рабочих. Были разработаны конструкции агломерационных чаш со значительно лучшими технологическими характеристиками. В 1914—1918 гг. на Днепровском заводе была построена аглофабрика с прямоугольными (стационарными) чашами системы Гриневальта, а в 1925 г. на Гороблагодатском руднике — фабрика с 28 круглыми чашами (диаметром 2,3 м) шведской фирмы AIB. Принципиально агломерационный процесс в чашах шёл так же, как и в котлах Геберлейна. Отличие состояло в том, что толщина спекаемого слоя была уменьшена до 250—300 мм, а дутьевой режим был заменён на вакуумный — воздух в слой засасывался сверху благодаря создаваемому вентиляторами разрежению под колосниковой решёткой. Поэтому зажигание (воспламенение частичек твердого топлива шихты) также производилось сверху. В прямоугольных чашах зажигание осуществляли с помощью передвижных зажигательных горнов с газовыми горелками[10].
Поскольку каждая из упомянутых агломерационных установок обладала теми или другими существенными недостатками (один из самых серьёзных — низкая производительность), ни чаши, ни трубчатые печи не получили широкого распространения в металлургии. Прорыв в области окускования руд был сделан двумя американскими инженерами А. Дуайтом и Р. Ллойдом, которые в 1906 г. разработали конструкцию, а в 1911 г. ввели в эксплуатацию первую конвейерную агломерационную машину непрерывного действия. Процесс спекания руд шел по тому же принципу, что и в котлах Геберлейна или в чашах, — тепло, необходимое для оплавления рудных зёрен, выделялось при слоевом сжигании частичек твёрдого топлива в результате просасывания воздуха через шихту, уложенную на колосниковую решётку. Успех в быстром и широком распространении агломерации как главного способа окускования железорудных материалов был предопределён очень удачной конструкцией агломерационной машины. Площадь спекания первой агломерационной машины Дуайта-Ллойда была 8,1 м2 (при ширине ленты 1,05 и длине 7,7 м); суточная производительность — 140 т агломерата при спекании колошниковой пыли[11].
В течение 1990-х годов неизмеримо выросли размеры агломерационных машин — площадь спекания увеличилась до 600 м2 и более: суточная производительность достигла 15 000—18 000 т агломерата. Изменились марки сталей, из которых изготовляются различные детали машин, но принципиальное устройство машин осталось без изменения[11].
Роль в процессах чёрной металлургии
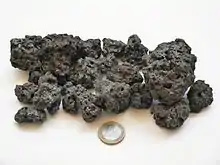
Агломерация железорудного концентрата (иногда в смеси с рудой, отходами металлургического производства) является заключительной операцией в комплексе мероприятий по подготовке железных руд к доменной плавке. Главная цель этой операции состоит в том, чтобы превратить мелкий рудный концентрат в более крупные куски — агломерат, использование которого в доменной плавке обеспечивает формирование слоя шихты хорошей газопроницаемости, что является непременным условием высокопроизводительной работы доменной печи.
Доменная плавка высокой интенсивности возможна при большом количестве сгорающего в горне доменной печи кокса, что, с одной стороны, ведет в выделению большого количества тепла, а с другой — к образованию в нижней части печи свободного пространства (благодаря газификации твердого кокса), куда опускается столб доменной шихты. Хорошая газопроницаемость шихты нужна для того, чтобы большой объем образующихся при горении кокса газов успевал проходить через межкусковые каналы слоя при относительно небольших перепадах давления газа между горном и колошником (150—200 кПа на высоте слоя шихты 20—25 м)[8].
Технология
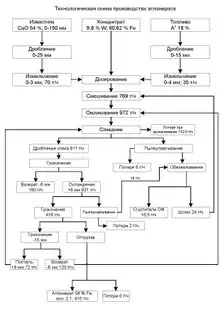
Состав шихты
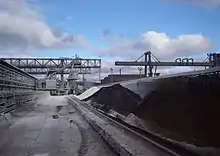
Общая схема агломерационного процесса методом просасывания включает в себя следующие этапы.
Типичная шихта, идущая на производство железорудного агломерата, состоит из следующих компонентов:
- мелкий железорудный материал, как правило, концентрат;
- измельченное топливо — кокс (фракция 0—3 мм), содержание в шихте 4—6 %;
- измельченный известняк (фракция 0—3 мм), содержание до 8—10 %;
- возврат — некондиционный агломерат от предыдущего спекания (фракция 0—8 мм), содержание 25—30 %;
- железосодержащие добавки — колошниковая пыль из доменных печей, окалина прокатных цехов, пиритные огарки сернокислотного производства и др. (фракция 0—3 мм), содержание до 5 %.
Отдозированные в заданном соотношении компоненты перемешивают, увлажняют (для улучшения окомкования) и после окомкования без уплотнения загружают на колосниковую решетку слоем 300—400 мм. Затем включают нагнетатель — вентилятор, работающий на отсос. Под колосниковой решеткой создается разрежение, благодаря которому в слой вначале засасывается поток горячих горновых газов, обеспечивающих «зажигание» шихты, то есть происходит нагрев поверхностного слоя примерно до 1200 °С (в течение 1,5—2,0 мин). Поступающий затем в слой в остальное время процесса атмосферный воздух обеспечивает интенсивное горение частиц кокса шихты. В зоне максимальных температур (1400—1450°С) происходит частичное плавление рудных зерен, их слипание, а затем в ходе последующей кристаллизации образуется пористая структура — агломерационный спёк.
Зональный режим
В каждый момент времени происходит воспламенение нагретых до 700—800 °С частичек топлива в слое шихты, примыкающем к нижней границе зоны горения. Одновременно заканчивается горение частиц топлива на верхней границе зоны горения. В результате этого зона горения, совмещенная с зоной плавления, непрерывно перемещается вниз, в направлении движения газового потока, как бы «внедряясь» в слой исходной шихты и оставляя за собой зону охлаждающегося агломерата.
Определяющей зоной процесса является горизонт с максимальной температурой — зона плавления — зона формирования агломерата. Выше этой зоны находится слой пористого агломерационного спёка. В расположенной ниже зоне интенсивного нагрева происходит быстрый нагрев спекаемого материала — со скоростью до 800 град/мин и такое же быстрое охлаждение продуктов горения. Выходя из этой зоны, газ с температурой 300—400 °С попадает во влажную шихту — образуется зона сушки. В этой зоне газ охлаждается до 50—60 °С и покидает её насыщенным парами воды. В расположенной ниже холодной шихте (15—20 °С) газ охлаждается, становится пересыщенным, и часть паров воды в этой зоне конденсации в виде капелек осаждается на комочках шихты, увеличивая их влагосодержание. Так как скорость движения зоны конденсации в несколько раз больше скорости перемещения по слою зоны сушки, между этими зонами со временем образуется слой переувлажненной шихты. При этом быстро уменьшается толщина слоя исходной шихты.
Общее время агломерации можно разбить на три периода:
- начальный, когда формируются основные зоны спекаемого слоя (в этот период осуществляется зажигание аглошихты, примерно за это же время происходит переувлажнение всего слоя шихты);
- основной период, когда тепловой и газодинамический режимы стабилизировались и происходит перемещение по слою зон формирования агломерата, интенсивного нагрева, сушки;
- заключительный, в течение которою последовательно «выклиниваются» все зоны спекаемого слоя, на ленте остается только охлаждающийся агломерационный спёк.
Процесс считается законченным, когда зона формирования агломерата дойдет до колосников спекательных тележек. При вертикальной скорости спекания 20 мм/мин слой шихты толщиной 300 мм превращается в агломерат за 15 мин.
Особенности процесса
Современный агломерационный процесс относится к типу слоевых, когда проходящий через спекаемый рудный материал воздух обеспечивает протекание двух главных процессов:
- горение твердого топлива шихты и
- осуществляет перенос тепла из одного элементарного слоя в другой.
В связи с этим высокие технико-экономические показатели агломерационного процесса могут быть достигнуты только при интенсивном поступлении воздуха в спекаемый слой. Между тем агломерационные шихты, содержащие пылевидные железорудные концентраты (с размером частиц менее 0,1 мм), обладают очень высоким газодинамическим сопротивлением. Поэтому обязательной подготовительной операцией является окомкование шихт — процесс формирования гранул размером 2—8 мм. Слой такой окомкованной, хорошо газопроницаемой шихты позволяет достичь высоких скоростей движения газового потока (до 0,5—0,6 м/с) при относительно небольших перепадах давлений над и под слоем (10—15 кПа).
Одной из характерных особенностей агломерации железорудных материалов является интенсивный тепло- и массообмен в слое шихты благодаря ее высокой удельной поверхности (30—50 см2/см3). Именно этим объясняется относительно небольшая высота (по 15—40 мм) зон плавления, интенсивного нагрева, сушки, конденсации. Следствием этой особенности процесса является небольшое время пребывания каждого элементарного объема спекаемого материала при высоких температурах — 1,5—2,0 мин. Поэтому технологи должны обеспечить такие условия (крупность частиц компонентов шихты, скорость движения газа в слое и др.), чтобы за это небольшое время успели пройти основные химико-минералогические и физические процессы, обеспечивающие получение агломерата требуемого качества: выгорание углерода и серы, диссоциация карбонатов, нагрев рудных частиц до температур плавления, их слипание и др.
Второй особенностью процесса агломерации является возникновение неоднородного температурного поля в объеме спекаемого материала. Из-за точечного распределения частичек топлива в шихте очаги горения-плавления чередуются с участками материала (шихты или спёка), находящимися в твердом состоянии. В результате локальной усадки расплавленного материала в очаге горения образуются поры размером 3—10 мм. Благодаря этой особенности сохраняется пористая достаточно газопроницаемая структура слоя в зоне существования расплавов. Дополнительные поры возникают при выделении газов от горения углерода, серы, диссоциации карбонатов, восстановления оксидов железа и др.
Третья особенность агломерации заключается в том, что горение частиц топлива в слое происходит в условиях двойной регенерации тепла: воздух, поступающий в зону горения, предварительно подогревается до 1000—1100 °С в слое охлаждающегося спёка, а топливо (и остальная часть шихты) перед воспламенением нагревается до 700—800 °С потоком горячих газов, выходящих из зоны горения. В течение примерно 80 % времени спекания выходящий из слоя газ имеет температуру 50—60 °С. Это значит, что основное количество тепла от зажигания и горения углерода твердого топлива шихты остается внутри слоя и участвует в теплообменных процессах.
Еще одна положительная особенность агломерации железорудных материалов состоит в том, что в результате частичного восстановления оксидов железа в зоне умеренных температур значительно снижаются температуры плавления таких восстановленных материалов — на 150—200 °С, благодаря чему существенно сокращается потребность в тепле на процесс — это позволяет снизить содержание топлива в шихте при сохранении достаточно высокой прочности агломерата. Указанное выше делает агломерацию методом просасывания исключительно эффективным процессом с точки зрения теплотехнических показателей: при содержании углерода в шихте всего 3—5 % удается нагревать спекаемый материал до 1400—1450 °С[13].
Сравнение с другими методами окускования
С 1955 г. в мировой металлургии в промышленных масштабах начали использовать новый метод окускования тонких железорудных концентратов — производство окатышей. При проплавке окатышей в доменных печах США удельный расход кокса сократился, а производительность печей увеличилась почти вдвое. Благодаря активной рекламной кампании, которую развернули фирмы-разработчики технологии и изготовители оборудования фабрик по производству окатышей, у многих металлургов сложилось впечатление, что окатыши обладают неоспоримыми преимуществами перед агломератом. В МЧМ СССР было принято решение, что стратегическим направлением развития подотрасли подготовки железорудного сырья к доменной плавке является интенсивное строительство фабрик по производству окатышей с постепенным сокращением, а в конечном счете с полной ликвидацией агломерационного производства. Любые попытки ученых и производственников в 60-х гг. ХХ века дать объективную оценку новому способу окускования решительно пресекались. Замалчивались результаты работы ряда доменных печей Японии на хорошо подготовленном офлюсованном агломерате по сравнению с проплавкой окатышей (неофлюсованных). Результаты такой тенденциозной технической политики не замедлили сказаться. Вскоре после начала использования в доменной плавке на ММК окатышей ССГОК пришлось аварийно останавливать доменные печи по причине интенсивного износа засыпных аппаратов и огнеупорной кладки, обусловленного значительным повышением содержания пыли в доменном газе из-за сильного разрушения окатышей в ходе доменной плавки.
Последовавший за этими событиями объективный анализ показал, что окатыши не являются «абсолютно» лучшим видом окускованного рудного сырья. Они обладают рядом серьезных недостатков по сравнению с агломератом:
- окатыши невозможно получать из относительно грубых концентратов, а дополнительное измельчение до необходимой крупности (-0,05 мм) значительно удорожает концентрат;
- окатыши сильнее агломерата разрушались в ходе восстановительных процессов;
- чрезвычайно трудно технологически получать окатыши повышенной (до 1,4—1,5) основности;
- при работе доменных печей только на окатышах возникают определенные затруднения из-за ухудшения газопроницаемости слоя и развития процессов шлакообразования.
Главным достоинством агломерации является универсальность — процесс спекания идет достаточно успешно с использованием рудных материалов в широком диапазоне по крупности (от 0 до 10 мм); допустимы некоторые отклонения от оптимальных параметров по влажности шихты, содержанию в ней твердого топлива и др.
Несомненным преимуществом окатышей перед агломератом является их хорошая транспортабельность: они мало разрушаются в ходе железнодорожных или морских перевозок. Таким образом, целесообразно окускование тонкого рудного концентрата производить путем производства окатышей в том случае, когда горно-рудный комбинат (с обогатительной фабрикой) находится на значительном удалении от металлургического завода.
Среди металлургов существует мнение, что агломерация и производство окатышей — не конкурирующие, а дополняющие друг друга методы окускования[14].
Примечания
- Коротич, 2009, с. 14.
- Козловский, 1984, с. 43.
- Коротич, 2000, с. 345—354.
- Коротич, 2000, с. 74.
- Коротич, 2000, с. 186.
- Козловский, 1984, с. 44.
- Коротич, 2009, с. 16.
- Коротич В. И., Фролов Ю. А., Бездежский Г. Н. Агломерация рудных материалов. — Екатеринбург: ГОУ ВПО «УГТУ-УПИ», 2003. — С. 16—17. — 400 с. — ISBN 5-321-00336-X.
- Коротич, 2009, с. 16—17.
- Коротич, 2009, с. 17.
- Коротич, 2009, с. 18.
- Коротич, 2009, с. 285.
- Коротич, 2009, с. 27—31.
- Коротич, 2009, с. 26—27.
Литература
- Вегман Е. Ф. Теория и технология агломерации. — М.: Металлургия, 1974. — 288 с.
- Коротич В. И., Фролов Ю. А., Каплун Л. И. Теоретические основы технологий окускования металлургического сырья. Агломерация: учебное пособие. — Екатеринбург: ГОУ ВПО УГТУ-УПИ, 2005. — 417 с.
- Коротич В. И., Фролов Ю. А., Каплун Л. И. Теоретические основы технологий окускования металлургического сырья. Агломерация: учебное пособие. — 2-е, исправл. и дополн.. — Екатеринбург: ГОУ ВПО УГТУ-УПИ, 2009. — 417 с. — ISBN 978-5-321-01579-7.
- Пузанов В. П., Кобелев В. А. Введение в технологию металлургического структурообразования. — Екатеринбург: УрО РАН, 2005. — 501 с.
- Гл. ред. Е. А. Козловский. Горная энциклопедия в пяти томах. Том 1. — Москва: Советская энциклопедия, 1984. — 560 с.
- Коротич В. И., Набойченко С. С., Сотников А. И., Грачев С. В., Фурман Е. Л., Ляшков В. Б. (под ред. В. И. Коротича). Начала металлургии: Учебник для вузов. — Екатеринбург: УГТУ, 2000. — 392 с. — ISBN 5-230-06611-3.