Жаропрочные сплавы
Жаропрочные сплавы — металлические материалы, обладающие высоким сопротивлением пластической деформации и разрушению при действии высоких температур и окислительных сред. Начало систематических исследований жаропрочных сплавов приходится на конец 1930-х годов — период нового этапа в развитии авиации, связанного с появлением реактивной авиации и газотурбинных двигателей (ГТД).
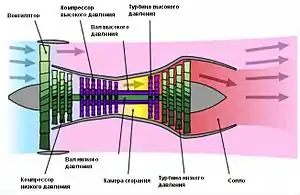
Жаропрочные сплавы могут быть на алюминиевой, титановой, железной, медной, кобальтовой и никелевой основах. Наиболее широкое применение в авиационных двигателях получили никелевые жаропрочные сплавы, из которых изготавливают рабочие и сопловые лопатки, диски ротора турбины, детали камеры сгорания и т. п. В зависимости от технологии изготовления никелевые жаропрочные сплавы могут быть литейными, деформируемыми и порошковыми. Наиболее жаропрочными являются литейные сложнолегированные сплавы на никелевой основе, способные работать до температур 1050—1100 °C в течение сотен и тысяч часов при высоких статических и динамических нагрузках[1].
История
Первые жаропрочные стали для газотурбинных двигателей были разработаны в Германии фирмой Krupp в 1936—1938 годах. Высоколегированная аустенитная сталь Тинидур создавалась как материал рабочих лопаток турбины на температуры 600—700 °C. Тинидур — аустенитная сталь с дисперсионным твердением (Ni3Ti) и карбидным упрочнением. В 1943—1944 годах годовое производство Тинидур составляло 1850 тонн. Институтом Deutsche Versuchsanstalt für Luftfahrt (DVL) и фирмой Heraeus Vacuumschmelze были разработаны аустенитые стали (сплавы по английской терминологии) DVL42 и DVL52 на более высокие рабочие температуры 750—800 °C. Составы сталей приведены в таблице.
Наименование | %C | %Mn | %Si | %Ni | %Co | %Cr | %Mo | %W | %Ti | %Al | % др. элементов |
---|---|---|---|---|---|---|---|---|---|---|---|
Тинидур | до 0,14 | 0,6-1,0 | 0,6-1,0 | 29,0-31,0 | 14,5-15,5 | 1,8-2,2 | 0,2 | Fe основа | |||
DVL42 | до 0,1 | 0,6-1,0 | 0,4-0,8 | 30-35 | 22-25 | 12-17 | 4-6 | 4-6 | 1,5-2,0 | Fe основа | |
DVL52 | до 0,1 | 0,6-1,0 | 0,4-0,8 | 30-35 | 22-25 | 12-17 | 4-6 | 4-6 | 4-5 %Ta | ||
Хромадур | 0,9-0,12 | 17,5-18,5 | 0,55-0,7 | 11,0-14,0 | 0,7-0,8 | V 0,60-0,70 0,18-0,23 N2 |
В Германии 1940-х годов среди разработчиков авиационных ГТД существовало стремление повысить температуру газа перед турбиной до 900 °C. С этой целью институт DVL совместно с рядом фирм экспериментировал с аустенитными сложнолегированными сплавами. В ходе войны была признана невозможность подобного решения по причине острого дефицита в Германии легирующих элементов. В результате исследования приняли два направления: 1. создание полых охлаждаемых воздухом лопаток (рабочих и сопловых) при соответствующем снижении легирования используемых материалов; 2. исследование возможностей керамических материалов. Оба направления работ являлись пионерскими, по каждому из них были получены значимые результаты.
Первые серии реактивного двигателя Jumo-004A выпускались с 1942 года с монолитными рабочими и сопловыми лопатками из материала Тинидур фирмы Крупп. Позднее заменены полыми охлаждаемыми лопатками из того же материала, что позволило повысить температуру газа перед турбиной до 850 °C (серия Jumo-004E). С 1944 года на серийных модификациях двигателя Jumo-004B применялись полые охлаждаемые рабочие лопатки из менее дефицитной стали Cromadur.
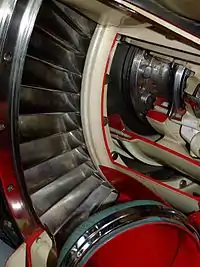
К 1942 году в Великобритании создан жаропрочный сплав Нимоник-80 — первый в серии высокожаропрочных дисперсионно-твердеющих сплавов на никель-хромовой основе. Создатель сплава — Уильям Гриффитс англ. Griffiths W.T.. Основа сплава Нимоник-80 — нихром (80 %Ni — 20 %Cr), известный с начала XX века своей высокой жаростойкостью и высоким электрическим сопротивлением. Ключевыми легирующими элементами сплава нимоник-80 являлись титан (2,5 %) и алюминий (1,2 %), образующие упрочняющую фазу. Количество упрочняющей гамма-штрих фазы в сплаве составляло 25-35 об%[5]. Нимоник-80 использовался в деформированном состоянии для изготовления рабочих лопаток турбины одного из первых газотурбинных двигателей Роллс-Ройс Нин (англ.), стендовые испытания которого начались в октябре 1944 года. Лопатки турбины из сплава нимоник-80 обладали высокой длительной прочностью при температурах 750—850 °C.
В СССР аналогами сплава нимоник-80 являются никелевые жаропрочные сплавы ЭИ437, ЭИ437А (ХН77ТЮ) и ЭИ437Б (ХН77ТЮР), срочным порядком созданные к 1948 году сотрудниками ВИАМ, ЦНИИЧермет и завода «Электросталь» при участии Ф. Ф. Химушина[6].
Основу жаропрочных сплавов, как правило, составляют элементы VIII группы таблицы Менделеева. До 1940-х годов основу жаропрочных сплавов составляли железо или никель. Добавлялось значительное количество хрома для увеличения коррозионной стойкости. Добавки алюминия, титана или ниобия увеличивали сопротивление ползучести. В некоторых случаях образовывались хрупкие фазы, такие, например, как карбиды M23C6. В конце 40-х годов прекратилось, в основном, использование железа как основы жаропрочных сплавов, предпочтение начали отдавать сплавам на основе никеля и кобальта. Это позволило получить более прочную и стабильную гранецентрированную матрицу.
В конце 1940-х годов была обнаружена возможность дополнительного упрочнения жаропрочных сплавов путём легирования молибденом. Позже для этой же цели начали применять добавки таких элементов, как вольфрам, ниобий, тантал, рений и гафний. (См. Карбид тантала-гафния, хотя в жаропрочных сплавах гафний не образует подобных карбидов, а повышает прочность и пластичность «механически», вызывая закручивание границ зёрен, т. н. «гафниевый эффект». Помимо этого, он участвует в образовании дополнительных количеств гамма-штрих фазы[7]).
Сплавы на основе никеля
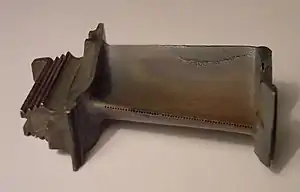
В 1950-х годах компаниями Pratt & Whitney и General Electric были разработаны сплавы Уаспалой и M-252, легированные молибденом и предназначенные для лопаток авиационных двигателей. Затем были разработаны такие сплавы, как Hastelloy alloy X, Rene 41, Инконель, в том числе Inco 718, Incoloy 901 и др.
Согласно оценкам экспертов, за период 1950—1980-х годов химические составы никелевых жаропрочных сплавов изменялись наиболее значительно за счет введения алюминия и замещающих его элементов в ' фазе. Указанное привело к увеличению объемной доли ' фазы от 25-35 об.% в сплавах нимоник 80 и U-700 до 65-70 об.% в современных лопаточных материалах[5].
Легирование
Жаропрочные сплавы на основе никеля, как правило, обладают сложным химсоставом. Он включает 12 — 13 компонентов, тщательно сбалансированных для получения необходимых свойств. Содержание таких примесей, как кремний (Si), фосфор (P), сера (S), кислород (O) и азот (N) также контролируется. Содержание таких элементов, как селен (Se), теллур (Te), свинец (Pb) и висмут (Bi) должно быть ничтожно малым, что обеспечивается подбором шихтовых материалов с низким содержанием этих элементов, так как избавиться от них в ходе плавки не представляется возможным. Эти сплавы обычно содержат 10—12 % хрома (Cr), до 8 % алюминия (Al) и титана (Ti), 5-10 % кобальта (Co), а также небольшие количества бора (B), циркония (Zr) и углерода (C). Иногда добавляются молибден (Mo), вольфрам (W), ниобий (Nb), тантал (Ta) и гафний (Hf).
Легирующие элементы в этих сплавах можно сгруппировать следующим образом:
- Элементы, образующие с Ni аустенитную -матрицу с гранецентрированной кристаллической решёткой — Co, Fe, Cr, Mo и W
- Элементы, образующие упрочняющую ' фазу (Ni3X) — Al, Ti, Nb, Ta, Hf. При этом Ti, Nb и Ta входят в состав фазы и упрочняют её.
- Элементы, образующие сегрегации по границам зёрен — B, C и Zr
К карбидообразующим элементам относятся Cr, Mo, W, Nb, Ta и Ti. Al и Cr образуют оксидные плёнки, защищающие изделия от коррозии.
Сплав | %Ni | %Cr | %Co | %Mo | %Al | %Ti | %Nb | %C | %B | Zr | % др. элементов |
---|---|---|---|---|---|---|---|---|---|---|---|
Inconel X-750 | 73,0 | 18,0 | - | - | 0,8 | 2,5 | 0,9 | 0,04 | - | - | 6,8 % Fe |
Udimet 500 | 53,6 | 18,0 | 18,5 | 4,0 | 2,9 | 2,9 | - | 0,08 | 0,006 | 0,05 | |
Udimet 700 | 53,4 | 15,0 | 18,5 | 5,2 | 4,3 | 3,5 | - | 0,08 | 0,03 | - | |
Waspaloy | 58,3 | 19,5 | 13,5 | 4,3 | 1,3 | 3,0 | - | 0,08 | 0,006 | 0,06 | |
Astroloy | 55,1 | 15,0 | 17,0 | 5,2 | 4,0 | 3,5 | - | 0,06 | 0,03 | - | |
Rene 41 | 55,3 | 19,0 | 11,0 | 10,0 | 1,5 | 3,1 | - | 0,09 | 0,005 | - | |
Nimonic 80A | 74,7 | 19,5 | 1,1 | - | 1,3 | 2,5 | - | 0,06 | - | - | |
Nimonic 90 | 57,4 | 19,5 | 18,0 | - | 1,4 | 2,4 | - | 0,07 | - | - | |
Nimonic 105 | 53,3 | 14,5 | 20,0 | 5,0 | 1,2 | 4,5 | - | 0,2 | - | - | |
Nimonic 115 | 57,3 | 15,0 | 15,0 | 3,5 | 5,0 | 4,0 | - | 0,15 | - | - |
Сплав | %Ni | %Cr | %Co | %Mo | %Al | %Ti | %Nb | %C | %B | Zr | % др. элементов |
---|---|---|---|---|---|---|---|---|---|---|---|
B-1900 | 64,0 | 8,0 | 10,0 | 6,0 | 6,0 | 1,0 | - | 0,10 | 0,015 | 0,1 | 4,0 % Ta |
MAR-M200 | 60,0 | 9,0 | 10,0 | - | 5,0 | 2.0 | 1.0 | 0,13 | 0,015 | 0,05 | 12,0 % W |
Inconel 738 | 61,0 | 16,0 | 8,5 | 1,7 | 3,4 | 3,4 | 0,9 | 0,12 | 0,01 | 0,10 | 1,7 % Ta, 3,6 % W |
Rene 77 | 58,0 | 14,6 | 15,0 | 4,2 | 4,3 | 3,3 | - | 0,07 | 0,016 | 0,04 | |
Rene 80 | 60,0 | 14,0 | 9,5 | 4,0 | 3,0 | 5,0 | - | 0,17 | 0,015 | 0,03 | 4,0 %W |
Фазовый состав
К основным фазам жаропрочных сплавов относятся:
- Гамма-фаза () является матрицей с г.ц.к. кристаллической решёткой. В твёрдом растворе этой фазы содержится большое количество Co, Cr, Mo, W
- Гамма-штрих (') фаза образует частицы преципитата, имеющего также г.ц.к. кристаллическую решётку. В эту фазу входят такие элементы, как Al и Ti. Объёмная доля этой фазы, когерентной аустенитной матрице достаточно велика
- Карбиды. Содержание углерода в сплавах относительно невелико (0,05-0,2 %). Он соединяется с карбидообразующими элементами — Ti, Ta, Hf
- Зернограничная '-фаза. Эта фаза образуется в виде плёнки по границам зёрен в процессе термической обработки.
- Бориды Выделяются по границам зёрен в виде редких частиц
- Фазы т. п. у. (топологически плотно упакованные фазы) имеют пластинчатую морфологию. Пример: фазы , и фаза Лавеса. Эти фазы приводят к охрупчиванию материала и являются нежелательными.
Термическая обработка
Деформируемые никелевые жаропрочные сплавы содержат в матрице дисперсные выделения карбидов типа MC. Гомогенизационный отжиг даёт возможность подготовить матрицу к получению равномерного распределения частиц упрочняющей фазы ' в процессе последующего старения. Для примера, для сплава Inco 718 гомогенизационный отжиг продлится в течение 1 часа при 768 °C, а старение проводится в два этапа: 8 часов при 718 °C и 8 часов при 621 °C. После гомогенизационного отжига важно выдержать скорость охлаждения, чтобы препятствовать выделению нежелательных фаз. Охлаждение между этапами старения проводится плавно в течение 2 часов.
Жаропрочность
Одним из факторов, определяющих жаропрочность, является высокое сопротивление ползучести. Жаропрочность сплавов оценивается пределами длительной прочности или ползучести при высоких температурах, и связана, в первую очередь, с их структурой и составом. По структуре жаропрочные сплавы должны быть многофазными с прочными границами зёрен и фаз[1]. В никелевых жаропрочных сплавах сказанное обеспечивается многокомпонентным легированием. При этом жаропрочность сплавов тем выше, чем больше объёмная доля упрочняющих фаз и чем выше их термическая стабильность, то есть устойчивость против растворения и коагуляции при повышении температуры.
Длительная прочность
Никелевые жаропрочные сплавы используются при температурах 760—980 °C. Литые жаропрочные сплавы имеют высокую длительную прочность при более высоких температурах. Например, сплав MAR-M246 имеет длительную прочность 124 МПа после 1000 часов выдержки при 982 °C.
Жаропрочные сплавы на никелево-железной основе используются при температурах 650—815 °C. Их длительная прочность намного ниже.
Сплав | 650 °C 100 часов |
650 °C 1000 часов |
815 °C 100 часов |
815 °C 1000 часов |
982 °C 100 часов |
982 °C 1000 часов |
---|---|---|---|---|---|---|
Inconel X-750 | 552 | 469 | 179 | 110 | 24 | |
Udimet 700 | 703 | 400 | 296 | 117 | 55 | |
Astroloy | 772 | 407 | 290 | 103 | 55 | |
IN-100 | 503 | 379 | 172 | 103 | ||
MAR-M246 | 565 | 448 | 186 | 124 |
Монокристаллические жаропрочные сплавы
В 1970—1980 годы началось применение литых жаропрочных сплавов, полученных методами направленной кристаллизации и монокристаллических сплавов на никелевой основе. Применение этих материалов (на никелевой основе) позволило увеличить прочность и термическую долговечность лопаток газовых турбин.
полученных методами направленной кристаллизации[9]
Сплав | %Cr | %Co | %W | %Mo | %Ta | %Nb | %Ti | %Al | %Hf | %B | %Zr | %C |
---|---|---|---|---|---|---|---|---|---|---|---|---|
MAR-M200+Hf | 9,0 | 10,0 | 12,0 | - | - | 1,0 | 2,0 | 5,0 | 2,0 | 0,015 | 0,08 | 0,14 |
MAR-M246+Hf | 9,0 | 10,0 | 10,0 | 2,5 | 1,5 | - | 1,5 | 5,5 | 1,5 | 0,015 | 0,05 | 0,15 |
MAR-M247 | 8,4 | 10,0 | 10,0 | 0,6 | 3,0 | - | 1,0 | 5,5 | 1,4 | 0,015 | 0,05 | 0,15 |
RENE 80H | 14,0 | 9,5 | 4,0 | 4,0 | - | - | 4,8 | 3,0 | 0,75 | 0,015 | 0,02 | 0,08 |
Сплав | %Cr | %Co | %W | %Mo | %Ta | %Nb | %Ti | %Al | %Hf |
---|---|---|---|---|---|---|---|---|---|
Pratt & Whitney № 1 | 10,0 | 5,0 | 4,0 | - | 12,0 | - | 1,5 | 5,0 | - |
Pratt & Whitney № 2 (3 % Re) |
5,0 | 10,0 | 6,0 | 2,0 | 8,7 | - | - | 5,6 | 0,1 |
CMSX-2 | 8,0 | 5,0 | 8,0 | 0,6 | 6,0 | - | 1,0 | 5,5 | - |
SRR99 | 8,5 | 5,0 | 9,5 | - | 2,8 | - | 2,2 | 5,5 | - |
Уже ранний опыт эксплуатации лопаток газотурбинных двигателей Jumo-004 показал (исследования К. Гебхардт, фирма Крупп, Эссен), что на практике срок службы лопаток определяется усталостной прочностью, и подавляющее число разрушений лопаток являются усталостными[10].
Сплавы на основе кобальта
Ещё в начале XX века компанией Хэйнс (англ. Haynes) были получены патенты на сплавы системы Co — Cr и Co — Cr — W. Эти сплавы, именуемые «стеллитами» использовались вначале для производства режущего инструмента. и износостойких деталей. В 1930-х годах был разработан литейный Co — Cr — Mo сплав для зубного протезирования Vitallium. Аналогичный по составу сплав HS-21 начал использоваться десятилетие спустя в турбонагревателях и газовых турбинах. Тогда же начали использовать сплав системы Co — Ni — Cr для направляющих лопаток газотурбинных двигателей. В 1943 г. был разработан литейный сплав Co — Ni — Cr — W (X-40) также применяемый при изготовлении лопаток. В 1950—1970 годы были разработаны новые никелевые жаропрочные сплавы, изготовленные путём вакуумной выплавки и упрочняемые за счёт выделения фазы '. Это привело к уменьшению использования сплавов на основе кобальта.
Особенности жаропрочных сплавов на кобальтовой основе
- Температура плавления у сплавов на кобальтовой основе — более высокая. По этой причине повышены характеристики длительной прочности. Эти жаропрочные сплавы могут работать при более высоких температурах, по сравнению со сплавами на основе никеля и железа
- Высокое содержание хрома повышает сопротивление горячей коррозии
- Сплавы характеризуются повышенным сопротивлением термической усталости и имеют хорошую свариваемость.
Дисперсноупрочненные жаропрочные сплавы
Важной проблемой в разработке конструкционных материалов с повышенной прочностью и пластичностью является обеспечение их стабильности и однородности физико-механических свойств во всем интервале температур эксплуатации от криогенных и вплоть до предплавильных температур. В настоящее время наиболее перспективным путем решения этой проблемы является упрочнение базового сплава дисперсными наночастицами тугоплавких оксидов. Такие материалы принято называть ODS (oxide dispersion strengthened) сплавами[11]. Базой для ODS-сплавов наиболее часто служат аустенитные жаропрочные сплавы на основе Ni, Cr и Fe. В качестве упрочняющих частиц, как правило, используют тугоплавкие оксиды Al2O3, TiO2, ThO2, La2O3, BeO и Y2O3. ODS- суперсплавы получают методом механического легирования, который включает следующие стадии: 1) совместное перемалывание в шаровых мельницах порошков исходных компонент суперсплава с добавлением мелкодисперсных конгломератов тугоплавкого оксида; 2) запайка дегазированного порошка в герметичный стальной контейнер; 3) компактирование экструзией; 4) горячая опрессовка; 5) зонная рекристаллизация. ODS- суперсплав (Inconel MA758) на основе оксида иттрия Y2O3 был разработан в 90-х годах прошлого века.
Диффузионные покрытия
Поскольку турбинные лопатки, изготовленные из литейных жаропрочных сплавов работают при высоких температурах и в агрессивной среде, возникает необходимость в их защите от горячей коррозии. С этой целью используют диффузионные покрытия двух типов, т. н. пакетная цементация и покрытия, наносимые в газовой фазе. В процессе покрытия происходит обогащение поверхностного слоя алюминием и образование алюминида никеля, как матрицы покрытия.
Процесс пакетной цементации
Процесс происходит при более низкой температуре (около 750 °C). Детали помещаются в коробки со смесью порошков: активный материал, содержащий алюминий и образующий покрытие, активатор (хлорид или фторид) и термический балласт, например, окись алюминия. При высокой температуре образуется газообразный хлорид (или фторид) алюминия, который переносится на поверхность изделия. Затем происходит распад хлорида алюминия и диффузия алюминия вглубь объема. Образуется т. н. «зелёное покрытие», очень хрупкое и тонкое. После этого проводится диффузионный отжиг (несколько часов при температурах около 1080 °C). При этом образуется окончательное покрытие.
Покрытие в газовой фазе
Процесс идёт при более высокой температуре около 1080 °C. Активный материал, содержащий алюминий, не находится в непосредственном контакте с изделием. Нет необходимости и в термическом балласте. Процесс отличается диффузией вовне. Также требуется диффузионный отжиг.
Плазменные покрытия
Более современной технологией защиты лопаток является плазменное напыление термобарьерных покрытий. Как правило, термобарьерное покрытие состоит из нескольких слоев — подслой, слой MeCrAlY, слой керамики (часто применяют оксид циркония, стабилизированный иттрием). Для разных двигателей аттестованы вакуумное или атмосферное плазменное напыление, однако все современные разработки выполняются на атмосферной плазме, как более дешевой в эксплуатации.
Примечания
- Авиация. Энциклопедия. М.: Большая Российская энциклопедия, 1994, с. 201
- Luft.-Forschung, Bd 18(1941), N 8, S. 275—279
- Pomp A., Krisch A.: Zur Frage der Dauerstandfestigkeit warmfester Staehle bei 600, 700 und 800 °C. Mitteilungen der KWI fuer Eisenforschung (Abhandl. 400), 1940
- Report on Visit to Germany and Austria to investigate Alloys for Use at High Temperature. BIOS Final Report N 396, London, 1946
- Giamei A.F., Pearson D.D., Anton D.L. Materials Research Society Symposium Proc. 1985, v. 39, pp. 293—307
- Туманов А. Т., Шалин Р. Е., Старков Д. П. Авиационное материаловедение. — в кн.: Развитие авиационной науки и техники в СССР. Историко-технические очерки. М.: Наука, 1980, с. 332—334
- Суперсплавы II под ред. Симса, Столоффа, Хагеля. Перевод на русский язык. М., Металлургия, 1995, т 1, стр. 29
- http://www.msm.cam.ac.uk/phase-trans/2003/nickel.html
- Superalloys
- Report on Visit to Germany and Austria to investigate Alloys for use at a High Temperatures/ - BIOS Final Report No 396. London 1946, p. 13.
- К.А. Ющенко, Ю.А. Семеренко, Е.Д. Табачникова, А.В. Подольский, Л.В. Скибина, С.Н. Смирнов, В.С. Савченко. Inconel MA758: новый наноструктурный суперсплав. Акустические и механические свойства в интервале температур 4,2—310 К // Металлофиз. новейшие технол. — 2013. — Т. 35, вып. 2. — С. 225-231.
Литература
- Суперсплавы II. Жаропрочные материалы для аэрокосмических и промышленных энергоустановок. — М.: «Металлургия», 1995.
- Строение и свойства авиационных материалов. — М.: «Металлургия», 1989.
- Лекции о суперсплавах на сайте университета Кембриджа.
- Химушин Ф. Ф. Жаропрочные стали и сплавы. — М.: «Металлургия», 1969.