Кирпич
Кирпич (др.-рус. кирпичь)[1][2] — штучное изделие предназначенное для устройства кладок[3]. Исторически — искусственный камень правильной формы, используемый в качестве строительного материала, произведенный из минеральных материалов, обладающий свойствами камня[4].
Кирпич | |
---|---|
![]() | |
Сделано из | глина, цемент и суглинок |
Код MCN | 6901.00.10 |
![]() |
Этимология
Слово «кирпич» заимствовано из тюркских языков[5], например, тур. kirpiǯ, тат. kirpič / кирпич, азерб. kärpχič[1][2]. До кирпича в Европе и на Руси использовалась плинфа (например, при посещении Иваном Грозным недостроенного Софийского собора в Вологде на него упала плинфа: «как из своду туповатова упадала плинфа красная»). «Плинфа» — тонкая и широкая прямоугольная глиняная пластина, толщиной примерно 2,5 см. Изготавливалась в специальных деревянных формах. Плинфа сушилась 10—14 дней, затем её обжигали в печи. На многих плинфах находят клейма, которые считаются клеймами изготовителя.
История
.jpg.webp)
Хотя вплоть до нашего времени широчайшее распространение имел во многих странах необожжённый кирпич-сырец, часто с добавлением в глину резаной соломы, применение в строительстве обожжённого кирпича также восходит к глубокой древности (постройки в Египте, 3—2 тысячелетие до н. э.). Особенно важную роль играл кирпич в зодчестве Месопотамии и Древнего Рима, где из кирпича (45×30×10 см) выкладывали сложные конструкции, в том числе арки, своды и тому подобное. Форма кирпичей в Древнем Риме варьировалась, использовались в том числе прямоугольные, треугольные и круглые в плане кирпичи[6], прямоугольные плиты кирпича радиально разрезали на 6—8 частей, что позволяло из получившихся треугольных кусков класть более прочную и фигурную кладку.
Стандартный обожжённый кирпич использовался на Руси с конца XV века. Ярким примером стало строительство стен и храмов Московского Кремля во времена Иоанна III, которым заведовали итальянские мастера. «… и кирпичную печь устроили за Андрониковым монастырем, в Калитникове, в чём ожигать кирпич и как делать, нашего Русского кирпича уже да продолговатее и твёрже, когда его нужно ломать, то водой размачивают. Известь же густо мотыками повелели мешать, как на утро засохнет, то и ножём невозможно расколупить».
Привычный же нам кирпич прямоугольной формы (его удобней было держать в руке) появился в Англии в XVI веке[7].
В коллекции кирпичей (англ. American Brick Collection), подаренной в 1994 году Рэймондом Чейзом Национальному музею строительства (англ. National Building Museum) в Вашингтоне, содержится 1800 различных кирпичей, произведённых в США в конце XIX — начале XX века и отмеченных клеймом производителя[8][9].
Общая характеристика
Классификация
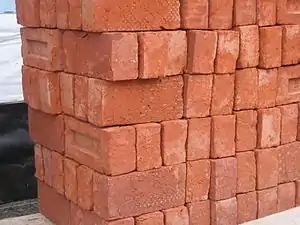
Виды кирпича по материалу:
- сырцовый кирпич — необожжённый кирпич из глины;
- керамический — из обожжённого сырца, обычно имеет красный цвет, наиболее распространённый тип кирпича[10];
- силикатный — из кварцевого песка (ок. 90 %) и извести[10];
- гиперпрессованный кирпич — из отсева известковых пород (мрамора, ракушечника, доломита, до 90 % состава кирпича) и портландцемента (6−8 %)[11].
Классификация кирпича по цели использования[10]:
- строительный или рядовой по ГОСТ 530—2007 (ГОСТ 530—2012);
- лицевой кирпич (облицовочный):
- фактурный с гладкими или неровными краями предназначен для облицовки фасадов зданий и обустройства заборов;
- фасонный — для кладки сложных форм вокруг окон, подоконников, арок, столбов, заборов, беседок;
- огнеупорный кирпич (печной, шамотный) по ГОСТ 390-96 — для объектов с постоянным воздействием высокой температуры;
- клинкерный кирпич — для облицовки стен, цоколей, мощения дорожек.
По способу изготовления и типу формовки[12]:
- кирпичи пластического формования формуют на прессах из глины влажностью 15−21 %;
- кирпичи полусухого формования прессуют из глины влажностью 8−14 %.
В зависимости от характера наполнения[10]:
- полнотелый кирпич — пустотелость в виде пор не превышает 12-13 %;
- пустотелый кирпич — имеет полости, полученные при формовке, применяют в основном для возведения перегородок, число полых камер от 2 до 10, у силикатного кирпича пористость бывает от 24 до 30 %, у керамического — до 45 %. Прочность на сжатие такая же, как у полнотелого кирпича, на изгиб — в несколько раз ниже.
Размеры кирпичей
Существуют разные стандарты размеров кирпича. Например, в Великобритании стандартный кирпич имеет размеры 215×102,5×65 мм. В Германии и на постсоветском пространстве основным стандартом считается 250×120×65 мм
Выделяют 2 основных формата кирпичей: керамические (ГОСТ 530—2012) и силикатные (ГОСТ 379—2015).
В России кирпичи единого стандарта (нормального формата — НФ[13]) появились в 1927 году. Одним из первых общесоюзных стандартов на кирпич был ОСТ 90035-39. Нормальный формат имеет габаритные размеры 250×120×65 мм. Наименования остальных размеров являются производными от НФ:
- 1 НФ (одинарный) — 250×120×65 мм;
- 1.4 НФ (полуторный) — 250×120×88 мм;
- 2.1 НФ (двойной) — 250×120×138 мм.
Изделия номинального размера 2.1 НФ и более называются керамическими камнями, размеры типовых моделей согласно ГОСТ 530—2012:
- 4.5 — 250×250×140 мм;
- 6.8 — 380×250×140 мм;
- 6.0 — 250×250×188 мм[14].
Неполномерный (часть):
- 3/4 — 180 мм;
- 1/2 — 120 мм;
- 1/4 — 60—65 мм.
Масса кирпичей
Масса кирпичей зависит в первую очередь от класса плотности изделия, всего выделяют 7 классов для керамического и силикатного кирпича.
Формула расчета массы: a*b*c*p, где первые 3 параметра — длина, ширина и толщина, p — общая плотность изделия.
Ориентировочная масса керамических кирпичей (ГОСТ 530—2012):
- полнотелый 250×120×65 мм (2 класс плотности): 3.315..3.705 кг;
- пустотелый 250×120×65 мм (1.4 класс плотности): 2.34..2.73 кг;
- полнотелый 250×120×88 мм (2 класс плотности): 4.488..5.016 кг;
- пустотелый 250×120×88 мм (1.4 класс плотности): 3.168..3.696 кг;
- полнотелый 250×120×140 мм (2 класс плотности): 7.038..7.866 кг;
- пустотелый 250×120×140 мм (1.4 класс плотности): 4.968..5.796 кг[15].
Названия сторон
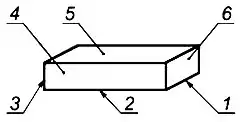
- Постель — рабочая сторона изделия, расположенная параллельно основанию кладки (на примере 1 НФ это часть с размерами 250×120 мм)[13].
- Ложок — средняя по площади сторона изделия, расположенная перпендикулярно к постели (у 1 НФ — 250×65 мм)[13].
- Тычок — наименьшая сторона изделия, расположенная перпендикулярно к постели (у 1 НФ — 120×65 мм)[13].
Кирпич с криволинейным ложком или тычком называется лекальным или фасонным.
Клейма на кирпиче
.jpg.webp)
Клеймо на кирпиче ставит завод-изготовитель. В старину производили кирпич ручной формовки. Старинный кирпич имеет различные клейма. Они могут быть выполнены в виде символов или букв. Как правило, это сокращение инициалов хозяина завода. При строительстве казённых предприятий завод, выигравший поставку, мог ставить клеймо в виде двуглавого орла. Такой старинный кирпич в народе получил название «имперский кирпич». В Санкт—Петербурге встречается самое большое количество различных клейм. На кирпичах можно встретить клеймо в виде ключа, короны, орла, якоря, подковы, название рек, городов и различных фамилий. На заводе клеймо могло видоизменяться. Зачастую заводы переходили от одного собственника к другому. Поэтому один и тот же завод мог за свою историю выпускать разнообразные клейма. Известны случаи, когда кирпичный завод переходил от отца к сыну и клеймо видоизменялось с сохранением фамилии, но изменением дизайна. Одним из самых известных заводов, выпускающих кирпичи с клеймом, был завод купцов Стрелиных.
Современный кирпич
Современное кирпичное производство ставит клейма на различных поверхностях кирпича (ложок, тычок, постель). В прошлых веках клеймо ставили в основном на постель.
Виды кирпича и их преимущества
Кирпич делится на две большие группы: красный и белый. Красный кирпич состоит в основном из глины, белый — из песка и извести. Смесь последнего была названа «силикатной», а отсюда и силикатный кирпич.
Силикатный кирпич
«Готовить» силикатный кирпич стало возможно только после развития новых принципов производства искусственных строительных материалов. В основе такого изготовления заложен так называемый автоклавный синтез: 9 долей кварцевого песка, 1 доля воздушной извести и добавки после полусухого прессования (таким образом создаётся форма кирпича) подвергаются автоклавной обработке (воздействие водяного пара при температуре 170—200 °С и давления 8—12 атм.). Если к этой смеси добавляются атмосферостойкие, щелочестойкие пигменты, то получается цветной силикатный кирпич.
Преимущества силикатного кирпича
- Экологичность Силикатный кирпич изготовлен из экологически чистого натурального сырья — извести и песка, по технологии, знакомой человечеству несколько столетий.
- Звукоизоляция. Это играет немаловажную роль при возведении межквартирных или межкомнатных стен. Силикатный кирпич применяют для кладки стен и столбов в гражданском и промышленном строительстве.
- Высокая морозостойкость и прочность. Силикатный кирпич по прочности и морозостойкости значительно превосходит марки легких бетонов. На построенные из него фасады строители дают гарантию 50 лет.
- Надёжность и широкий ассортимент. Надёжность и широкий ассортимент силикатного кирпича позволяет использовать его как в новом строительстве, так и при реконструкции. Фактурный, цветной силикатный кирпич украсит фасады как общественных, жилых зданий, так и загородных коттеджей, дач.
- Тип окраски. Цветной силикатный кирпич окрашивается в массе так же, как и керамический кирпич. Но, в отличие от керамического кирпича, окраска силикатного может производиться только с помощью специальных искусственных красителей, а керамический кирпич приобретает определённый цвет в результате смешения разных сортов глины.
- Неприхотливость. Строения из силикатного кирпича неприхотливы и устойчивы ко внешним факторам. Капризы природы не оказывают существенного влияния на его внешний вид, Фасад сохраняет цвет и не требует дополнительного ухода, за исключением случаев использования в агрессивных средах или в условиях повышенной влажности.
- Цена[16]
Недостатки силикатного кирпича
- Серьёзным недостатком силикатного кирпича является пониженная водостойкость и жаростойкость, поэтому его нельзя использовать в конструкциях, подвергающихся воздействию воды (фундаменты, канализационные колодцы и др.) и высоких температур (печи, дымовые трубы и др.).
Применение силикатного кирпича
Силикатный кирпич обычно применяется для возведения несущих и самонесущих стен и перегородок, одноэтажных и многоэтажных зданий и сооружений, внутренних перегородок, заполнения пустот в монолитно-бетонных конструкциях, наружной части дымовых труб.
Керамический кирпич
Керамический кирпич обычно применяется для возведения несущих и самонесущих стен и перегородок, одноэтажных и многоэтажных зданий и сооружений, внутренних перегородок, заполнения пустот в монолитно-бетонных конструкциях, кладки фундаментов, внутренней части дымовых труб, промышленных и бытовых печей.
Керамический кирпич подразделяется на рядовой (строительный) и лицевой. Последний применяется практически во всех областях строительства.
Лицевой кирпич изготавливается по специальной технологии, которая придаёт ему массу преимуществ. Лицевой кирпич должен быть не только красивым, но и надёжным. Облицовочный кирпич обычно применяется при возведении новых зданий, но также с успехом может быть использован и в различных реставрационных работах. Его используют при облицовке цоколей здaний, стен, заборов, для внутреннего дизайна.
Преимущества керамического рядового кирпича
- Прочен и износостоек. Керамический кирпич обладает высокой морозостойкостью, что подтверждается многолетним опытом его применения в строительстве.
- Хорошая звукоизоляция — стены из керамического кирпича, как правило, соответствуют требованиям [СП] 51.13330.2011 «Защита от шума»..
- Низкое влагопоглощение (менее 14 %, а для клинкерного кирпича этот показатель может достигать 3 %) — Более того, керамический кирпич быстро высыхает.
- Экологичность Керамический кирпич изготовлен из экологически чистого натурального сырья — глины, по технологии, знакомой человечеству десятки веков. Во время эксплуатации построенных из него зданий, красный кирпич не выделяет вредных для человека веществ, таких как газ радон.
- Устойчивость почти ко всем климатическим условиям, что позволяет сохранять надёжность и внешний вид.
- Высокая прочность (15 МПа и выше — 150 атм.).
- Высокая плотность (1950 кг/м³, до 2000 кг/м³ при ручной формовке).
Преимущества керамического облицовочного кирпича
- Морозостойкость. Облицовочный кирпич обладает высокой морозостойкостью, а для северного климата это особенно важно. Морозостойкость кирпича является наряду с прочностью важнейшим показателем его долговечности. Керамический облицовочный кирпич идеально подходит для российского климата.
- Прочность и устойчивость. Благодаря высокой прочности и малому объёму пористости кладка, возводимая из облицовочных изделий, отличается высокой прочностью и поразительной устойчивостью к воздействию окружающей среды.
- Различная фактура и цветовая гамма. Диапазон различных форм и цветов облицовочного кирпича даёт возможность создания имитации старинных построек при возведении современного дома, а также позволит возместить утраченные фрагменты фасадов старинных особняков.
Недостатки керамического кирпича
- Высокая цена. В связи с тем, что керамический кирпич требует несколько этапов обработки, его цена довольно высокая, по сравнению с ценой силикатного кирпича.
- Возможность появления высолов. В отличие от силикатного кирпича, керамический кирпич «требует» качественный раствор, в противном случае могут появляться высолы.
- Необходимость приобретать весь требуемый облицовочный кирпич из одной партии. Если облицовочный керамический кирпич приобретается из разных партий, могут возникнуть проблемы с тоном.
Технология производства
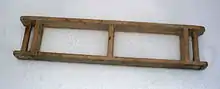
До XIX века техника производства кирпичей оставалась примитивной и трудоёмкой. Формовали кирпичи вручную, сушили исключительно летом, а обжигали в напольных печах-времянках, выложенных из высушенного кирпича-сырца. В середине XIX века были изобретены кольцевая обжиговая печь и ленточный пресс, обусловившие переворот в технике производства. В конце XIX века стали строить сушилки. В это же время появились глинообрабатывающие машины: бегуны, вальцы, глиномялки.
В наше время более 80 % всего кирпича производят предприятия круглогодичного действия, среди которых имеются крупные механизированные заводы, производительностью свыше 200 млн штук в год.
Организация кирпичного производства
Керамический кирпич
Необходимо создание условий для обеспечения основных параметров производства:
- постоянного или среднего состава глины;
- равномерной работы производства.
В кирпичном производстве результата добиваются только после длительных экспериментов с режимами сушки и обжига. Эта работа должна проводиться при постоянных основных параметрах производства.
Глина
.jpg.webp)
Хороший (лицевой) керамический кирпич производится из глины, добытой мелкой фракцией с постоянным составом минералов. Месторождения с однородным составом минералов и многометровым слоем глины, пригодным для добычи одноковшовым экскаватором, очень редки и почти все разработаны.
Большинство месторождений содержит многослойную глину, поэтому лучшими механизмами, способными при добыче делать глину среднего состава, считаются многоковшовый и роторный экскаваторы. При работе они срезают глину по высоте забоя, измельчают её, и при смешивании получается средний состав. Другие типы экскаваторов не смешивают глину, а добывают её глыбами.
Постоянный или средний состав глины необходим для подбора постоянных режимов сушки и обжига. Для каждого состава нужен свой режим сушки и обжига. Один раз подобранные режимы позволяют получать высококачественный кирпич из сушилки и печи годами.
Качественный и количественный состав месторождения выясняется в результате разведки месторождения. Только разведка выясняет минеральный состав: какие суглинки пылеватые, глины легкоплавкие, глины тугоплавкие и т. д. содержатся в месторождении.
Лучшими глинами для производства кирпича считаются те глины, которые не требуют добавок. Для производства кирпича обычно используется глина, непригодная для других керамических изделий.
Сушилки камерные
Сушилки загружаются кирпичом полностью, и в них постепенно изменяется температура и влажность по всему объёму сушилки, в соответствии с заданной кривой сушки изделий.
Сушилки туннельные
Сушилки загружаются постепенно и равномерно. Вагонетки с кирпичом продвигаются через сушилку и проходят последовательно зоны с разной температурой и влажностью. Туннельные сушилки лучше всего применять для сушки кирпича из сырья среднего состава. Применяются при производстве однотипных изделий строительной керамики. Очень хорошо «держат» режим сушки при постоянной и равномерной загрузке кирпича-сырца.
Процесс сушки
Глина — это смесь минералов, состоящая по массе более чем на 50 % из частиц до 0,01 мм. К тонким глинам относятся частицы менее 0,2 мкм, к средним 0,2—0,5 мкм и крупнозернистым 0,5—2 мкм. В объёме кирпича-сырца есть множество капилляров сложной конфигурации и разных размеров, образованных глинистыми частицами при формовке.
Глины дают с водой массу, которая после высыхания сохраняет форму, а после обжига приобретает свойства камня. Пластичность объясняется проникновением воды, хорошей природной смазки, между отдельными частицами минералов глины. Свойства глины с водой важны при формовке и сушке кирпича, а химический состав определяет свойства изделий во время обжига и после обжига.
Чувствительность глины к сушке зависит от процентного соотношения «глинистых» и «песчаных» частиц. Чем больше в глине «глинистых» частиц, тем труднее удалить воду из кирпича-сырца без образования трещин при сушке и тем больше прочность кирпича после обжига. Пригодность глины для производства кирпича определяется лабораторными испытаниями.
Если в начале сушилки в сырце образуется много паров воды, то их давление может превысить предел прочности сырца и появится трещина. Поэтому температура в первой зоне сушилки должна быть такой, чтобы давление паров воды не разрушало сырец. В третьей зоне сушилки прочность сырца достаточна для повышения температуры и увеличения скорости сушки.
Режимные характеристики сушки изделий на заводах зависят от свойств сырья и конфигурации изделий. Существующие на заводах режимы сушки нельзя рассматривать как неизменные и оптимальные. Практика многих заводов показывает, что длительность сушки можно значительно сокращать, пользуясь методами ускорения внешней и внутренней диффузии влаги в изделиях.
Кроме того, нельзя не учитывать свойства глиняного сырья конкретного месторождения. Именно в этом и заключается задача заводских технологов. Нужно подобрать такую производительность линии формовки кирпича и режимы работы сушилки кирпича, при которых обеспечивается высокое качество сырца при максимально достижимой производительности кирпичного завода.
Процесс обжига
Глина представляет смесь легкоплавких и тугоплавких минералов. При обжиге легкоплавкие минералы связывают и частично растворяют тугоплавкие минералы. Структура и прочность кирпича после обжига определяется процентным соотношением легкоплавких и тугоплавких минералов, температурой и продолжительностью обжига.
В процессе обжига керамического кирпича легкоплавкие минералы образуют стекловидную, а тугоплавкие кристаллическую фазы. С повышением температуры всё более тугоплавкие минералы переходят в расплав, возрастает содержание стеклофазы. С увеличением содержания стеклофазы повышается морозостойкость и снижается прочность керамического кирпича.
При увеличении длительности обжига возрастает процесс диффузии между стекловидной и кристаллической фазами. В местах диффузии возникают большие механические напряжения, так как коэффициент термического расширения тугоплавких минералов больше коэффициента термического расширения легкоплавких минералов, что и приводит к резкому снижению прочности.
После обжига при температуре 950—1050 °C доля стекловидной фазы в керамическом кирпиче должна составлять не более 8—10 %. В процессе обжига подбираются такие температурные режимы обжига и продолжительность обжига, чтобы все эти сложные физико-химические процессы обеспечивали максимальную прочность керамического кирпича.
Песок
Основным компонентом силикатного кирпича (85-90 % по массе) является песок, поэтому заводы силикатного кирпича размещают, как правило, вблизи месторождений песка, и песчаные карьеры являются частью предприятий. Состав и свойства песка определяют во многом характер и особенности технологии силикатного кирпича.
Песок — это рыхлое скопление зёрен различного минерального состава размером 0,1 — 5 мм. По происхождению пески разделяют на природные и искусственные. Последние, в свою очередь, разделяют на отходы при дроблении горных пород (хвосты от обогащения руд, высевки щебеночных карьеров и т. п.), дробленые отходы от сжигания топлива (песок из топливных шлаков), дробленые отходы металлургии (пески из доменных и ватержакетных шлаков).
Форма и характер поверхности зерен песка имеют большое значение для формуемости силикатной смеси и прочности сырца, а также влияют на скорость реакции с известью, начинающейся во время автоклавной обработки на поверхности песчинок.
При грубой шихтовке песков в карьере проверяют, в какой пропорции загружают вагонетки или автосамосвалы песками различной крупности в каждом забое. При наличии нескольких приемных бункеров для разных фракций песка необходимо проверять заданную пропорцию песков в шихте по количеству питателей одинаковой производительности, одновременно выгружающих пески различной крупности.
Песок, поступающий из забоя до его употребления в производство, должен быть отсеян от посторонних примесей — камней, комочков глины, веток, металлических предметов и т. п. Эти примеси в процессе производства вызывают брак кирпича и даже поломки машин, поэтому над песочными бункерами устанавливают барабанные грохоты.
Известь

Известь является второй составной частью сырьевой смеси, необходимой для изготовления силикатного кирпича.
Сырьём для производства извести являются карбонатные породы, содержащие не менее 95 % углекислого кальция CaCO3. К ним относятся известняк плотный, известняковый туф, известняк-ракушечник, мел, мрамор. Все эти материалы представляют собой осадочную горную породу, образовавшуюся главным образом в результате отложения на дне морских бассейнов продуктов жизнедеятельности животных организмов.
Известняк состоит из известкового шпата-кальцита и некоторого количества различных примесей: углекислого магния, солей железа, глины и др. От этих примесей зависит окраска известняка. Обычно он бывает белым или разных оттенков серого и жёлтого цвета. Если содержание глины в известняках более 20 %, то они носят название мергелей. Известняки с большим содержанием углекислого магния называются доломитами.
Мергель является известково-глинистой породой, которая содержит от 30 до 65 % глинистого вещества. Следовательно, наличие в нём углекислого кальция составляет всего 35-70 %. Понятно, что мергели совершенно не пригодны для изготовления из них извести и поэтому не применяются для этой цели.
Доломиты, так же как известняки, относятся к карбонатным горным породам, состоящим из минерала доломита (СаСО3•МgСО3). Так как содержание в них углекислого кальция менее 55 %, то для обжига на известь они также непригодны. При обжиге известняка на известь употребляют только чистые известняки, не содержащие большого количества вредных примесей в виде глины, окиси магния и др.
По размерам кусков известняки для обжига на известь делятся на крупные, средние и мелкие. Содержание мелочи в известняке определяют, просеивая породу через грохоты.
Основным вяжущим материалом для производства силикатных изделий является строительная воздушная известь. По химическому составу известь состоит из окиси кальция (СаО) с примесью некоторого количества окиси магния (МgО).
Различают два вида извести: негашеную и гашеную; на заводах силикатного кирпича применяется негашеная известь. При обжиге известняк под влиянием высокой температуры разлагается на углекислый газ и окись кальция и теряет 44 % своего первоначального веса. После обжига известняка получается известь комовая (кипелка), имеющая серовато-белый, иногда желтоватый цвет.
При взаимодействии комовой извести с водой происходят реакции гидратации СаО + Н2О = Са(ОН)2, МgО + Н2О = Мg(ОН)2 или, по-другому — гашение извести. Реакции гидратации окисей кальция и магния идут с выделением тепла. Комовая известь (кипелка) в процессе гидратации увеличивается в объёме и образует рыхлую, белого цвета, легкую порошкообразную массу гидрата окиси кальция Са(ОН)2. Для полного гашения извести необходимо добавлять к ней воды не менее 69 %, то есть на каждый килограмм негашеной извести расходуется около 700 грамм воды. В результате получается совершенна сухая гашеная известь (пушонка). Её так же называют воздушной известью. Если гасить известь с избытком воды, получается известковое тесто.
Известь нужно хранить только в крытых складских помещениях, предохраняющих её от воздействия влаги. Не рекомендуется длительное время хранить известь на воздухе, так как в нём всегда содержится небольшое количество влаги, которая гасит известь. Содержание в воздухе углекислого газа приводит к карбонизации извести, то есть соединению с углекислым газом и тем самым частичному снижению её активности.
Силикатная масса
Известково-песчаную смесь готовят двумя способами: барабанным и силосным.
Силосный способ приготовления массы имеет значительные экономические преимущества перед барабанным, так как при силосовании массы на гашение извести не расходуется пар. Кроме того, технология силосного способа производства значительно проще технологии барабанного способа. Подготовленные известь и песок непрерывно подаются питателями в заданном соотношении в одновальную мешалку непрерывного действия и увлажняются водой. Перемешанная и увлажненная масса поступает в силосы, где выдерживается от 4 до 10 часов, в течение которых известь гасится.
Силос представляет собой цилиндрический сосуд из листовой стали или железобетона; высота силоса 8-10 м, диаметр 3,5-4 м. В нижней части силос имеет конусообразную форму. Силос разгружается при помощи тарельчатого питателя на ленточный транспортёр. При этом происходит большое выделение пыли.
При вылёживании в силосах масса часто образует своды; причина этого — относительно высокая степень влажности массы, а также уплотнение и частичное твердение её при вылёживании. Наиболее часто своды образуются в нижних слоях массы, у основания силоса. Для лучшей разгрузки силоса необходимо сохранять возможно меньшую влажность массы. Силосы разгружаются удовлетворительно лишь при влажности массы в 2 — 3 %. Силосная масса при выгрузке более пылит, чем масса, полученная по барабанному способу; отсюда более тяжелые условия для работы обслуживающего персонала.
Работа силоса протекает следующим образом: внутри силос разделен перегородками на три секции. Масса засыпается в одну из секций в течение 2,5 часов, столько же требуется и для разгрузки секции. К моменту заполнения силоса нижний слой успевает вылежаться в течение того же времени, то есть около 2,5 часов. Затем секция выстаивается 2,5 часа, и после этого её разгружают. Таким образом, нижний слой гасится около 5 часов.
Так как разгрузка силосов происходит только снизу, а промежуток между разгрузками составляет 2,5 часа, то и все последующие слои также выдерживаются в течение 5 часов в непрерывно действующих силосах.
Прессование кирпича-сырца
На качество кирпича и его прочность наиболее существенно влияет давление, которому подвергается силикатная масса во время прессования. В результате прессования происходит уплотнение силикатной массы.
Процесс прессования кирпича складывается из следующих основных операций: наполнения прессовых коробок массой, прессования сырца, выталкивания сырца на поверхность стола, снятия сырца со стола, укладки сырца на запарочные вагонетки.
После прессования полученные кирпичи автоматом-укладчиком укладываются на вагонетки, которые транспортируются в автоклавы, где производится тепло-влажная обработка кирпича.
Автоклавная обработка
Для придания необходимой прочности силикатному кирпичу его обрабатывают насыщенным паром. Полный технологический цикл запаривания кирпича в автоклаве состоит из операций очистки и загрузки автоклава, закрывания и закрепления крышек, перепуска пара; впуска острого пара, выдержки под давлением, второго перепуска, выпуска пара в атмосферу, открывания крышек и выгрузки автоклава. Совокупность всех перечисленных операций составляет цикл работы автоклава, который равен 10—13 часов.
Из автоклава силикатный кирпич поступает на открытую площадку, где складируется и отгружается потребителям.
Биокирпич
Изготавливается из биоцемента в ходе микробиологической преципитации карбоната кальция[17]. Для его получения используются бактерии Sporosarcina pasteurii, песок, хлорид кальция и мочевина.
В строительстве
Используется в виде редкого материала для строительства домов. Декоративный строительный материал, изготавливается из хвойных пород древесины. Применяется для облицовки жилых и хозяйственных зданий, используется в строительстве при укладке несущих стен и межкомнатных перегородок.
См. также
Примечания
- Кирпич . Этимологический онлайн-словарь русского языка Макса Фасмера. ΛΓΩ. Дата обращения: 10 февраля 2020.
- Кирпич . Этимологический онлайн-словарь русского языка Крылова Г. А.. ΛΓΩ. Дата обращения: 10 февраля 2020.
- ГОСТ Р 58033-2017 Здания и сооружения. Словарь. Часть 1. Общие термины п. 6.4.50
- ГОСТ Р 56891.6-2017 Сохранение объектов культурного наследия. Термины и определения. Часть 6. Каменное зодчество п. 89
- Кирпич // Этимологический словарь русского языка = Russisches etymologisches Wörterbuch : в 4 т. / авт.-сост. М. Фасмер ; пер. с нем. и доп. чл.‑кор. АН СССР О. Н. Трубачёва. — Изд. 2-е, стер. — М. : Прогресс, 1986. — Т. II : Е — Муж. — С. 238.
- Peet, Stephen Denison. The American Antiquarian and Oriental Journal, (Google Books), Jameson & Morse [etc.]: 1911, с. 35-36.
- д/ф «История кирпича» из серии Грандиозные изобретения канала 24Techno
- American Brick Collection. Gift of Raymond Chase (англ.). National Building Museum. Дата обращения: 27 марта 2017.
- Elif Sungur. Cityscapes Revealed: Highlights from the Collection (англ.) (недоступная ссылка). Dexigner (6 февраля 2006). Дата обращения: 27 марта 2017. Архивировано 30 марта 2017 года.
- БРЭ, 2009.
- В.Г. Киреев, В.В. Лукьяненко, Б.Г. Печеный. Перспективы производства и применения гиперпрессованного облицовочного кирпича (PDF). Северо-Кавказский Государственный Технический Университет (2004). Дата обращения: 30 января 2010. Архивировано 16 апреля 2012 года.
- Н. Г. Василовская, И. Г. Енджиевская, Г. П. Баранова, С. В. Дружинкин, Основы технологии строительной керамики и искусственных пористых заполнителей — Красноярск : СФУ, 2016. — 200 с. — ISBN 978-5-7638-3420-8 С. 28.
- ГОСТ 530-2012, 2013.
- Таблица размеров кирпичей согласно нормативам .
- Таблица массы кирпичей и плотность классов .
- Средние цены на приобретенные строительными организациями основные виды материалов по Российской Федерации в 1996—2011 гг.
- Роман Фишман Бригада бактерий // Популярная механика. — 2017. — № 6. — С. 25 — 26.
Литература
- Кирпич / Л. Б. Кирчо, А. Я. Щетенко, Я. М. Паромов, С. И. Баранова, К. Н. Попов // Киреев — Конго. — М. : Большая российская энциклопедия, 2009. — С. 43. — (Большая российская энциклопедия : [в 35 т.] / гл. ред. Ю. С. Осипов ; 2004—2017, т. 14). — ISBN 978-5-85270-345-3.
- Кирпич строительный // Товарный словарь. Том 3 / Гл. ред. И.А. Пугачев. — М.: Госторгиздат, 1957. — Стб. 549—555
- Пронженко В.В. Кирпич настоящий // Сделай сам : журнал. — М.: Знание, 2003. — № 1. — С. 100—106.
- Нормативная литература
- ГОСТ 379-95 Кирпич и камни силикатные : Технические условия. — М. : Стандартинформ, 1996.
- ГОСТ 530-2012 Кирпич и камень керамические : Общие технические условия : Официальное издание : [дата введения 2013-07-01] [заменяет ГОСТ 530-2007] / Разработан Ассоциацией производителей керамических материалов, ООО ВНИИСТРОМ «НЦК». — М. : Стандартинформ, 2013. — III+27, [3] с.
- ГОСТ 379-2015 Кирпич, камни, блоки и плиты перегородочные силикатные : Общие технические условия. — М. : Стандартинформ, 2015.