Ультразвуковая дефектоскопия
Ультразвукова́я дефектоскопи́я — метод, предложенный С. Я. Соколовым в 1928 году и основанный на исследовании процесса распространения ультразвуковых колебаний с частотой 0,5 — 25 МГц в контролируемых изделиях с помощью специального оборудования — ультразвукового преобразователя и дефектоскопа[1]:125. Является одним из самых распространённых методов неразрушающего контроля.
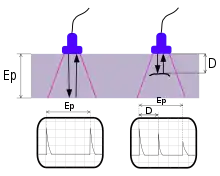
Принцип работы
Звуковые волны не изменяют траектории движения в однородном материале. Отражение акустических волн происходит от границы раздела сред с различными удельными акустическими сопротивлениями. Чем больше различаются акустические сопротивления, тем большая часть звуковых волн отражается от границы раздела сред. Так как включения в металле обычно содержат газ (смесь газов) возникающих вследствие процесса сварки, литья и т. п. И не успевают выйти наружу при затвердевании металла, смесь газов имеет на пять порядков меньшее удельное акустическое сопротивление, чем сам металл, то отражение будет практически полное.
Разрешающая способность акустического исследования, то есть способность выявлять мелкие дефекты раздельно друг от друга, определяется длиной звуковой волны, которая в свою очередь зависит от частоты ввода акустических колебаний. Чем больше частота, тем меньше длина волны. Эффект возникает из-за того, что при размере препятствия меньше четверти длины волны, отражение колебаний практически не происходит, а доминирует их дифракция. Поэтому, как правило, частоту ультразвука стремятся повышать. С другой стороны, при повышении частоты колебаний быстро растёт их затухание, что сокращает возможную область контроля. Практическим компромиссом стали частоты в диапазоне от 0,5 до 10 МГц.
Возбуждение и приём ультразвука
Существует несколько методов возбуждения ультразвуковых волн в исследуемом объекте. Наиболее распространённым является использование пьезоэлектрического эффекта. В этом случае излучение ультразвука производится с помощью преобразователя, который преобразует электрические колебания в акустические путём обратного пьезоэлектрического эффекта. Пройдя через контролируемую среду, ультразвуковые колебания попадают на приёмную пьезопластину преобразователя и, вследствие прямого пьезоэлектрического эффекта вновь становятся электрическими, которые и регистрируются измерительными цепями. В зависимости от конструкции и подключения, пьезопластины преобразователя могут выполнять роль только излучателя ультразвуковых колебаний или только приёмника, либо совмещать в себе обе функции.
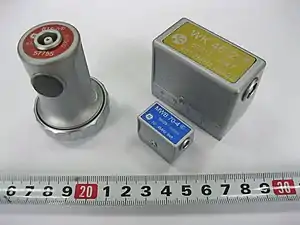
Также используются электромагнитно-акустический (ЭМА) метод, основанный на приложении сильных переменных магнитных полей к металлу. КПД этого метода гораздо ниже, чем у пьезоэлектрического, но зато может работать через воздушный зазор и не предъявляет особых требований к качеству поверхности.
Классификация методов исследования
Существующие акустические методы неразрушающего контроля подразделяют на две большие группы — активные и пассивные.
Активные
Активные методы контроля подразумевают под собой излучение и приём акустических волн.
Отражения

- Эхо-метод или эхо-импульсный метод — наиболее распространённый: преобразователь генерирует колебания (то есть выступает в роли генератора) и он же принимает отражённые от дефектов эхо-сигналы (приёмник). Данный способ получил широкое распространение за счёт своей простоты, так как для проведения контроля требуется только один преобразователь, следовательно при ручном контроле отсутствует необходимость в специальных приспособлениях для его фиксации (как, например, в дифракционно-временном методе) и совмещении акустических осей при использовании двух преобразователей. Кроме того, это один из немногих методов ультразвуковой дефектоскопии, позволяющий достаточно точно определить координаты дефекта, такие как глубину залегания и положение в исследуемом объекте (относительно преобразователя).
- Зеркальный или Эхо-зеркальный метод — используются два преобразователя с одной стороны детали: сгенерированные колебания отражаются от дефекта в сторону приёмника. На практике используется для поиска дефектов расположенных перпендикулярно поверхности контроля, например трещин.
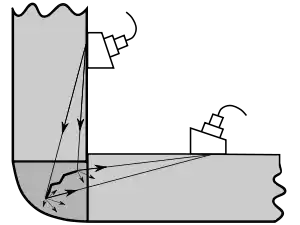
- Дифракционно-временной метод — используется два преобразователя с одной стороны детали, расположенные друг напротив друга. Если дефект имеет острые кромки (как, например, трещины) то колебания дифрагируют на концах дефекта и отражаются во все стороны, в том числе и в сторону приёмника. Дефектоскоп регистрирует время прихода обоих импульсов при их достаточной амплитуде. На экране дефектоскопа одновременно отображаются оба сигнала от верхней и от нижней границ дефекта, тем самым можно достаточно точно определить условную высоту дефекта. Способ достаточно универсален, позволяет производить ультразвуковой контроль на швах любой сложности, но требует специального оборудования для фиксации преобразователей, а также дефектоскоп, способный работать в таком режиме. Кроме того, дифрагированные сигналы достаточно слабые.
- Дельта-метод — разновидность зеркального метода — отличается механизмом отражения волны от дефекта и способом принятия сигнала. В диагностике используется для поиска специфично расположенных дефектов. Данный метод очень чувствителен к вертикально-ориентированным трещинам, которые не всегда удаётся выявить обычным эхо-методом.

- Ревербационный метод — основан на постепенном затухании сигнала в объекте контроля. При контроле двухслойной конструкции, в случае качественного соединения слоёв, часть энергии из первого слоя будет уходить во второй, поэтому ревербация будет меньше. В обратном случае будут наблюдаться многократные отражения от первого слоя, так называемый лес. Метод используется для контроля сцепления различных видов наплавок, например баббитовой наплавки с чугунным основанием. Основным недостатком данного метода является регистрация дефектоскопом эхо-сигналов от границы соединения двух слоёв. Причиной этих эхо-сигналов является разница скоростей упругих колебаний в материалах соединения и их различное удельное акустическое сопротивление. Например на границе баббит-сталь возникает постоянный эхо-сигнал даже в местах качественного сцепления. В силу конструкционных особенностей некоторых изделий, контроль качества соединения материалов ревербационным методом может быть невозможен именно из-за наличия на экране дефектоскопа эхо-сигналов от границы соединения.
- Акустическая микроскопия благодаря повышенной частоте ввода ультразвукового пучка и применению его фокусировки, позволяет обнаруживать дефекты, размеры которых не превышают десятых долей миллиметра. Широкое применение в промышленности затруднено в связи с крайне низкой производительностью метода. Данный метод подходит для исследовательских целей, диагностике, а также радиоэлектронной промышленности.
- Когерентный метод — по сути является разновидностью Эхо-импульсного метода. Помимо двух основных параметров эхо-сигнала, таких как амплитуда и время прихода, используется дополнительно фаза эхо-сигнала. Использование когерентного метода, а точнее нескольких идентичных преобразователей, работающих синфазно. При использовании специальных преобразователей, таких как преобразователь бегущей волны или его современный аналог — преобразователь с фазированной решёткой. Исследования применимости данного метода к реальным объектам контроля ещё не завершены. Метод находится на стадии научно-исследовательских изысканий.
Прохождения
Методы прохождения подразумевают под собой наблюдение за изменением параметров ультразвуковых колебаний, прошедших через объект контроля, так называемых сквозных колебаний. Изначально для контроля применялось непрерывное излучение, а изменение его амплитуды сквозных колебаний расценивалось как наличие дефекта в контролируемом объекте, так называемой звуковой тени. Отсюда появилось название теневой метод. Со временем непрерывное излучение сменилось импульсным, а к фиксируемым параметрам помимо амплитуды добавились также фаза, спектр и время прихода импульса и появились другие методы прохождения. Термин теневой потерял свой первоначальный смысл и стал означать один из методов прохождения. В англоязычной литературе метод прохождения называется through transmission technique или through transmission method, что полностью соответствует его российскому названию. Термин теневой в англоязычной литературе не применяется.
- Теневой — используются два преобразователя, которые находятся по две стороны от исследуемой детали на одной акустической оси. В данном случае один из преобразователей генерирует колебания (генератор), а второй принимает их (приёмник). Признаком наличия дефекта будет являться значительное уменьшение амплитуды принятого сигнала, или его пропадание (дефект создаёт акустическую тень).
- Зеркально-теневой — используется для контроля деталей с двумя параллельными сторонами, развитие теневого метода: анализируются отражения от противоположной грани детали. Признаком дефекта, как и при теневом методе, будет считаться пропадание отражённых колебаний. Основное достоинство этого метода в отличие от теневого заключается в доступе к детали с одной стороны.

- Временной теневой основан на запаздывании импульса во времени, затраченного на огибание дефекта. Используется для контроля бетона или огнеупорного кирпича.
- Метод многократной тени аналогичен теневому, с тем исключением, что ультразвуковая волна несколько раз проходит через параллельные поверхности изделия.
- При эхо-сквозном методе используют два преобразователя, расположенные по разные стороны объекта контроля друг напротив друга. В случае отсутствия дефекта, на экране дефектоскопа наблюдают сквозной сигнал и сигнал, двукратно отражённый от стенок объекта контроля. При наличии полупрозрачного дефекта, также наблюдают отражённые сквозные сигналы от дефекта.
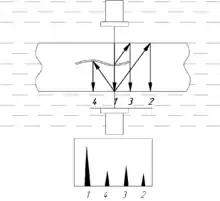
- Ревербационно-сквозной метод включает в себя элементы ревербационного метода и метода многократной тени. На небольшом расстоянии друг от друга, как правило, с одной стороны изделия, устанавливают два преобразователя — передатчик и приёмник. Ультразвуковые волны, посылаемые в объект контроля после многократных отражений, в конечном счёте попадают на приёмник. Отсутствие дефекта позволяет наблюдать стабильные отражённые сигналы. При наличии дефекта изменяется распространение ультразвуковых волн — изменяется амплитуда и спектр принятых импульсов. Метод применяется для контроля многослойных конструкций и полимерных композитных материалов.
- Велосиметрический метод основан на регистрации изменения скорости упругих волн в зоне дефекта. Применяется для контроля многослойных конструкций и для изделий из полимерных композиционных материалов.
Собственных колебаний
Основаны на возбуждении в объекте контроля свободных или вынужденных колебаний и измерению их параметров: собственных частот и величины потерь.
Вынужденных колебаний
- Интегральный
- Локальный
- Акустико-топографический
Свободных колебаний
Свободные колебания возбуждают путём кратковременного воздействия на объект контроля, после чего объект колеблется в отсутствии внешних воздействий. Источником кратковременного воздействия может быть любой механический удар, например молотком.
- Интегральный
- Локальный
Импедансные
- Изгибных волн
- Продольных волн
- Контактного импеданса
Пассивные
Пассивные методы контроля заключаются в приёме волн, источником которых является сам объект контроля.
- Акустико-эмиссионный
- Вибрационно-диагностический
- Шумодиагностический
Современные дефектоскопы точно замеряют время, прошедшее от момента излучения до приёма эхо-сигнала, тем самым измеряя расстояние до отражателя. Это позволяет добиться высокого лучевого разрешения исследования. Компьютеризированные системы позволяют провести анализ большого числа импульсов и получить трёхмерную визуализацию отражателей в металле.
Преимущества
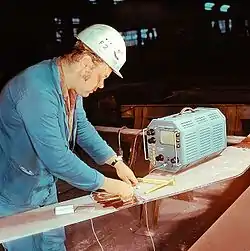
Ультразвуковой контроль не разрушает и не повреждает исследуемый образец, что является его главным преимуществом. Возможно проводить контроль изделий из разнообразных материалов, как металлов, так и неметаллов. Кроме того можно выделить высокую скорость исследования при низкой стоимости и опасности для человека (по сравнению с рентгеновской дефектоскопией) и высокую мобильность ультразвукового дефектоскопа.
Недостатки
Использование пьезоэлектрических преобразователей требует подготовки поверхности для ввода ультразвука в металл, в частности создания шероховатости поверхности не ниже класса 5, в случае со сварными соединениям ещё и направления шероховатости (перпендикулярно шву). Ввиду большого акустического сопротивления воздуха, малейший воздушный зазор может стать непреодолимой преградой для ультразвуковых колебаний. Для устранения воздушного зазора, на контролируемый участок изделия предварительно наносят контактные жидкости, такие как вода, масло, глицерин. При контроле вертикальных или сильно наклонённых поверхностей необходимо применять густые контактные жидкости с целью предотвращения их быстрого стекания.
Для контроля изделий с внешним диаметром менее 200 мм, необходимо использовать преобразователи, с радиусом кривизны подошвы R, равным 0,9-1,1R радиуса контролируемого объекта, так называемые притёртые преобразователи, которые в таком виде непригодны для контроля изделий с плоскими поверхностями. Например для контроля цилиндрической поковки, необходимо производить перемещение преобразователя в двух взаимно перпендикулярных направлениях, что подразумевает под собой использование двух притёртых преобразователей — по одному для каждого из направлений.
Как правило ультразвуковая дефектоскопия не может дать ответ на вопрос о реальных размерах дефекта, лишь о его отражательной способности в направлении приемника. Эти величины коррелируют, но не для всех типов дефектов. Кроме того, некоторые дефекты практически невозможно выявить ультразвуковым методом в силу их характера, формы или расположения в объекте контроля.
Практически невозможно производить достоверный ультразвуковой контроль металлов с крупнозернистой структурой, таких как чугун или аустенитный сварной шов (толщиной свыше 60 мм)[2][3] из-за большого рассеяния и сильного затухания ультразвука. Кроме того, затруднителен контроль малых деталей или деталей со сложной формой. Также затруднён ультразвуковой контроль сварных соединений из разнородных сталей (например аустенитных сталей с перлитными сталями) ввиду крайней неоднородности металла сварного шва и основного металла.
Применение

Применяется для поиска дефектов материала (поры, волосовины, различные включения, неоднородная структура и пр.) и контроля качества проведения работ — сварка, пайка, склейка и пр. Ультразвуковой контроль является обязательной процедурой при изготовлении и эксплуатации многих ответственных изделий, таких как части авиационных двигателей, трубопроводы атомных реакторов или железнодорожные рельсы.
Ультразвуковой контроль сварных швов
Сварные швы являются самой массовой областью применения ультразвуковой дефектоскопии. Это достигается за счёт мобильности ультразвуковой установки, высокой производительности контроля, точности, чувствительности к внутренним (объёмным — поры, металлические и неметаллические включения; плоскостным — непровары, трещины), а также внешним, то есть поверхностным дефектам сварных швов.
Многие ведомственные документы подразумевают обязательный ультразвуковой контроль сварных швов, либо альтернативный выбор ультразвукового или радиационного контроля, либо контроль обоими методами.
Основным документом в России по ультразвуковому контролю сварных швов является ГОСТ Р 55724-2013, в котором рассмотрены в полном объёме методы контроля стыковых, тавровых, нахлесточных и угловых сварных соединений, выполненных различными способами сварки. Также в нём подробно описаны калибровочные образцы (меры) СО-2 (СО-2А) и СО-3 и настроечные образцы, необходимые для настройки дефектоскопа, а также их параметры для их изготовления.
Объёмы контроля и нормы оценки качества сварного соединения устанавливаются различными нормативными документами в соответствии с требованиями прочности к конкретной сварной конструкции. На предприятиях, изготавливающих особо ответственные изделия, а также различными надзорными органами могут выпускаться собственные методические материалы для оценки качества сварных швов[4]. Примером может служить РД РОСЭК-001-96, разработанный Российской экспертной компанией по объектам повышенной опасности «РосЭК», и утверждённый Ростехнадзором для оценки качества сварных соединений для грузоподъёмных машин.
Нормативно-техническая документация
- ГОСТ Р 55724-2013 Контроль неразрушающий. Соединения сварные. Методы ультразвуковые.
- ГОСТ 24507-80 Контроль неразрушающий. Поковки из чёрных и цветных металлов. Методы ультразвуковой дефектоскопии.
- ГОСТ 22727-88 Прокат листовой. Методы ультразвукового контроля.
- ГОСТ 21120-75 Прутки и заготовки круглого и прямоугольного сечения. Методы ультразвуковой дефектоскопии.
- РД РОСЭК-001-96 Машины грузоподъёмные. Конструкции металлические. Контроль ультразвуковой. Основные положения.
- ОП 501 ЦД-97 Энергетическое оборудование. Сосуды давления. Трубопроводы пара, воды.
- ПНАЭ Г-7-010-89 Оборудование и трубопроводы атомных энергетических установок. Сварные соединения и наплавки. Правила контроля.
- ПНАЭ Г-10-032-92 Правила контроля сварных соединений элементов локализующих систем безопасности атомных станций.
- ПНАЭ Г-7-032-91 Унифицированные методики контроля основных материалов полуфабрикатов), сварных соединений и наплавки оборудования и трубопроводов атомных энергетических установок. Ультразвуковой контроль. Часть IV. Контроль сварных соединений из сталей аустенитного класса.
Примечания
- В. Н. Волченко, А. К. Гурвич, А. Н. Майоров, Л. А. Кашуба, Э. Л. Макаров, М. Х. Хусанов. Контроль качества сварки / Под ред. В. Н. Волченко. — Учебное пособие для машиностроительных вузов. — М.: Машиностроение, 1975. — 328 с. — 40 000 экз.
- ПНАЭ Г-7-032-91 Ультразвуковой контроль. Часть IV. Контроль сварных соединений из сталей аустенитного класса. П.1.4.
- Клюев В. В. Неразрушающий контроль. Том 3.: Справочник. В 7-и книгах / Под ред. Клюева В. В. — М.: Машиностроение, 2004.
- Некоторые «болезненные» вопросы УЗК традиционными методами // В мире неразрушающего контроля", 2013 — № 2(60)
Литература
- Шрайбер Д. С. Ультразвуковая дефектоскопия //М.: Металлургия. — 1965. — Т. 392. — С. 29.
- Гурвич А. К., Ермолов И. Н. Ультразвуковая дефектоскопия сварных швов — Киев: Техника, 1972, 460 с.
- Выборнов Б. И. Ультразвуковая дефектоскопия — М.: Металлургия, 1985.
- Щербинский В. Г., Паврос С. К., Гурвич А. К. Ультразвуковая дефектоскопия: вчера, сегодня, завтра //В мире неразрушающего контроля. — 2002. — №. 4. — С. 18.
- Ермолов И. Н. Достижения в теоретических вопросах ультразвуковой дефектоскопии, задачи и перспективы //Дефектоскопия. — 2004. — №. 10. — С. 13-48.
- Кретов Е. Ф. Ультразвуковая дефектоскопия в энергомашиностроении. — Изд.3-е, перераб.и доп. -Санкт-Петербург: СВЕН, 2011, 312с., ISBN 978-5-91161-014-2
- Марков А. А., Шпагин Д. А. Ультразвуковая дефектоскопия рельсов, — Изд. 2-е, исправл. и доп. — СПб.: Образование — Культура, 2013, 283с., ISBN 5-88857-104-0
Ссылки
- Электронный архив журнала «Дефектоскопия» по ультразвуковым методам.