Свеча зажигания
Свеча зажигания, Запальная свеча[1] — устройство для воспламенения топливо-воздушной смеси в самых разнообразных тепловых двигателях. Классфицируются как искровые, дуговые, накаливания, каталитические, полупроводниковые поверхностного разряда, плазменные воспламенители и другие. В бензиновых двигателях внутреннего сгорания используются (наиболее распространённые) искровые свечи зажигания. Воспламенение топливо-воздушной смеси в них производится электрическим разрядом напряжением в несколько тысяч или десятков тысяч вольт, возникающим между электродами свечи. Напряжение на свечу подаётся на каждом цикле, в определённый момент работы двигателя. В ракетных двигателях свеча зажигает топливную смесь электрическим разрядом только в момент запуска. Чаще всего, в процессе работы свеча изнашивается и должна периодически заменяться.
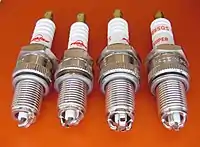
.JPG.webp)
В газотурбинных двигателях свеча воспламеняет струю топлива, выходящего из топливной форсунки в момент запуска, серией мощных дуговых разрядов. После этого горение факела топлива поддерживается самостоятельно. Используются, как правило, свечи поверхностного разряда, питающиеся высокочастотным током высокого напряжения от агрегата зажигания. Свечей чаще всего две (для надёжности), каждая установлена в воспламенителе со специальной пусковой форсункой, работающей только при запуске, что защищает свечу от обгорания при работе двигателя.[2][3] Калильные и одновременно каталитические свечи используются в модельных двигателях внутреннего сгорания. Топливная смесь двигателей специально содержит компоненты, которые легко воспламеняются в начале работы от раскалённой проволочки свечи. В дальнейшем накал нити поддерживается каталитическим окислением паров спирта, входящего в смесь.
История
Первая свеча зажигания в ее современном виде была разработана немецким инженером и ученым Робертом Бошем в 1902 году. Впервые свеча зажигания была использована с магнето высокого напряжения, также разработанным в мастерской компании BOSCH. Свечи зажигания BOSCH стали использоваться в двигателях внутреннего сгорания Карла Бенца, заменив используемые в то время калильные трубки с открытым пламенем. С тех пор и по настоящее время практически все свечи зажигания используют тот же принцип работы и строение, как и в 1902 году, эволюция данного узла шла преимущественно по пути усовершенствования используемых материалов (для изолятора, проводников и т.п.) и технологии изготовления (удешевления).
Устройство свечей зажигания
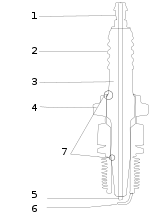
1 — контактный вывод
2 — рёбра изолятора
3 — изолятор
4 — металлическая оправа
5 — центральный электрод
6 — боковой электрод
7 — уплотнитель
Свеча зажигания состоит из металлического корпуса, изолятора и центрального проводника. Cвечи могут иметь встроенный резистор между контактным выводом и центральным электродом.
Контактный вывод
Контактный вывод, расположенный в верхней части свечи, предназначен для подключения свечи к высоковольтным проводам системы зажигания или непосредственно к индивидуальной высоковольтной катушке зажигания. Могут встречаться несколько слегка различных вариантов конструкции. Наиболее часто провод к свече зажигания имеет защёлкивающийся контакт, который надевается на вывод свечи. В других типах конструкции провод может крепиться к свече гайкой. Часто вывод свечи делают универсальным: в виде оси с резьбой и навинчивающегося защёлкивающегося контакта.
Рёбра изолятора
Рёбра изолятора затрудняют электрический пробой по его поверхности, удлиняя путь поверхностных токов (эквивалент более длинному изолятору).
Изолятор
Изолятор, как правило, делается из алюминиево-оксидной керамики, которая должна выдерживать температуры от 450 до 1 000 °C и напряжение до 60 000 В[уточнить]. Точный состав изолятора и его длина частично определяют тепловую маркировку свечи.
Часть изолятора, непосредственно прилегающая к центральному электроду, наиболее сильно влияет на качество работы свечи зажигания. Применение керамического изолятора в свече предложено Г. Хонольдом вследствие перехода к высоковольтному зажиганию.
Уплотнители
Предназначены для предотвращения прорыва горячих газов из камеры сгорания.
Корпус («юбка»)
Служит для ввёртывания свечи в резьбу головки блока цилиндров, для отвода тепла от изолятора и электродов, а также является проводником электричества от «массы» автомобиля к боковому электроду.
Боковой электрод
Как правило, изготавливается из легированной никелем и марганцем стали. Приваривается контактной сваркой к корпусу. Боковой электрод, зачастую, очень сильно нагревается во время работы, что может привести к калильному зажиганию. Некоторые конструкции свечей используют несколько боковых электродов. Для увеличения долговечности электроды дорогих свечей снабжают напылением из платины и других благородных металлов. Заявленный ресурс таких автомобильных свечей до 100.000 км, применение тем выгоднее, что в некоторых V-образных двигателях, расположенных поперёк, замена свечей довольно трудоёмка.
С 1999 года на рынке появлялись свечи нового поколения — так называемые плазменно-форкамерные свечи, где роль бокового электрода играет сам корпус свечи, снабженный специальным жаропрочным полусферическим насадком. При этом образуется кольцевой (коаксиальный) искровой зазор, где искровой заряд перемещается по кругу и форкамера, в которой происходит первичное воспламенение смеси. Такая конструкция как будто обеспечивает большой ресурс и самоочистку электродов, которые постоянно продуваются.
Эффективность «форкамерных» свечей вызывает ожесточенные споры как среди специалистов, так и среди рядовых автомобилистов. Не остаются в стороне и автомобильные журналы, часто в пылу дискуссии путают форкамерные свечи с многочисленными "самодельными свечами", выполненных путем доработки традиционных свечей. Чаще всего незначительно дорабатывается центральный или боковой электроды. Был проведен эксперимент, который показал, что подобные изменения формы электродов (сверление отверстия, раздвоение) практически бесполезны. Нет данных о комплектации современных автомобилей такими свечами, производители подобной продукции пишут, что их свечи подходят к любому автомобилю.
Центральный электрод
Центральный электрод как правило соединяется с контактным выводом свечи через стеклогерметик с резистором, это позволяет уменьшить радиопомехи от системы зажигания. Наконечник центрального электрода изготавливают из железо-никелевых сплавов с добавлением меди и хрома. Иногда на рабочую поверхность напыляют иттрий, в некоторых используют платиновые напайки или утонченный электрод из иридия. Обычно центральный электрод — наиболее горячая деталь свечи. Кроме того, центральный электрод должен обладать хорошей способностью к эмиссии электронов, для облегчения искрообразования (предполагается, что искра проскакивает в той фазе импульса напряжения, когда центральный электрод служит катодом). Поскольку напряжённость электрического поля максимальна вблизи краёв электрода, искра проскакивает между острым краем центрального электрода и краем бокового электрода. В результате этого края электродов подвергаются наибольшей электрической эрозии. Раньше свечи периодически вынимали и удаляли следы эрозии наждаком. Сейчас, благодаря применению сплавов с редкоземельными и благородными металлами (иттрий, иридий, платина), нужда в зачистке электродов практически отпала. Срок службы при этом существенно вырос.
Зазор
Зазор — минимальное расстояние между центральным и боковым электродом.
Величина зазора — это компромисс между «мощностью» искры, то есть размерами плазмы, возникающей при пробое воздушного зазора и между возможностью пробить этот зазор в условиях сжатой воздушно-бензиновой смеси.
Факторы, определяемые зазором:
- Чем больше зазор — тем больше размеры искры, тем больше вероятность воспламенения смеси и больше зона воспламенения. Всё это положительно влияет на потребление топлива, равномерность работы, понижает требования к качеству топлива, повышает мощность. Слишком увеличивать зазор тоже нельзя, иначе высокое напряжение может пробить высоковольтные провода на корпус, «бегунок» распределителя и т. д.
- Чем больше зазор — тем сложнее пробить его искрой. Пробоем изоляции называют потерю изоляцией изоляционных свойств при превышении напряжением некоторого критического значения, называемого пробивным напряжением . Соответствующая напряжённость электрического поля , где — расстояние между электродами, называется электрической прочностью промежутка. То есть чем больше зазор — тем бо́льшее напряжение пробоя необходимо. Там есть ещё зависимость от ионизации молекул, равномерности структуры вещества, полярности искры, скорости нарастания импульса, но это не важно в данном случае. Понятное дело, что высокое напряжение пр мы не можем поменять — оно определяется системой зажигания. А вот зазор мы поменять можем.
- Напряжённость поля в зазоре определяется формой электродов. Чем они острее — тем больше напряжённость поля в зазоре и легче пробой (как у иридиевых и платиновых свечей с тонким центральным электродом).
- Пробиваемость зазора зависит от плотности газа в зазоре. В нашем случае — от плотности воздушно-бензиновой смеси. Чем она больше — тем сложнее пробить. Пробивное напряжение газового промежутка с однородным и слабо неоднородным электрическим полем зависит как от расстояния между электродами, так и от давления и температуры газа. Эта зависимость определяется законом Пашена, согласно которому пробивное напряжение газового промежутка с однородным и слабо неоднородным электрическим полем определяется произведением относительной плотности газа на расстояние между электродами, . Относительной плотностью газа называют отношение плотности газа в данных условиях к плотности газа при нормальных условиях (20 °C, 760 мм рт. ст.).
- От зазора зависит соотношение между энергией, выделяемой в фазе пробоя, в дуговой фазе, и фазе тлеющего разряда. При увеличении зазора доля энергии пробоя растёт, и именно энергия, выделенная в фазе пробоя, определяет скорость сгорания. Поэтому на быстроходных двигателях зазор приходится увеличивать[4].
Зазор свечей не является константой, один раз заданной. Он может и должен подстраиваться под конкретную ситуацию эксплуатации двигателя. При переоборудовании автомобиля под более дешевое альтернативное топливо - сжиженный и сжатый газ (LPG, CNG), искровой зазор следует уменьшить из-за большего пробивного напряжения, чем у бензиновой смеси.
Режимы работы свечей
Искровые свечи бензиновых двигателей по режиму работы условно подразделяют на «горячие», «холодные», «средние» — в зависимости от тепловой характеристики свечи, выражаемой её калильным числом.
Калильное число свечи зажигания определяется на специальной тарировочной установке, имеющей вид эталонного одноцилиндрового двигателя определённой конструкции. В этот двигатель устанавливают соответствующую свечу зажигания и испытывают его в различных режимах, отслеживая при этом характер работы, а также температуру и давление в цилиндре.
Каждому режиму работы двигателя соответствует определённое значение температуры теплового конуса изолятора свечи. Когда эта температура поднимается выше 850…900°С, в двигателе начинает происходить так называемое калильное зажигание — самопроизвольное, без искры, воспламенение рабочей смеси при контакте с раскалённым тепловым конусом изолятора и другими частями свечи. Данный процесс обычно проявляется при работе двигателя на больших оборотах под нагрузкой. Он может приводить к оплавлению поршня и камеры сгорания, прогоранию поршней и выпускных клапанов, а также повреждению иных элементов двигателя. Для его предотвращения в двигатель устанавливаются свечи зажигания с «холодной» тепловой характеристикой, что обеспечивается хорошим отводом тепла от теплового конуса изолятора свечи. У таких свечей тепловой конус короткий и изолятор почти на всей своей длине контактирует с металлом корпуса свечи, благодаря чему тепло от него хорошо отводится и его перегрева не происходит даже в форсированных моторах с напряжённым тепловым режимом.
С другой стороны, однако, нельзя допускать и слишком малой рабочей температуры теплового конуса свечи, поскольку при её снижении ниже 400…500°С на конусе начинается накопление отложений, вследствие чего происходит поверхностная утечка тока высокого напряжения через слой нагара, что уменьшает мощность искрового пробоя зазора, или вообще делает его невозможным. Поэтому в менее форсированных двигателях применяются «горячие» свечи, у которых тепловой конус изолятора имеет большую длину и теплоотвод от него затруднён, благодаря чему даже при невысокой тепловой напряжённости камеры сгорания происходит нагрев свечей и их выход на рабочую температуру, обеспечивающую самоочищение от продуктов сгорания топливной смеси — нагара, сажи и т. п.
Изоляторы свечей, работающих в оптимальном режиме, всегда имеют цвет «кофе с молоком», говорящий о правильной работе двигателя. Стоит отметить, что прогрев свечей до температуры самоочищения занимает достаточно много времени и происходит лишь примерно после 10 км пробега автомобиля, в особенности по скоростной трассе, когда тепловыделение велико. При поездках на более короткие расстояния, а также работе двигателя исключительно на малых и средних оборотах, самоочищения свечей не происходит и они покрываются нагаром, требуя периодической очистки (механической или пескоструйной).
Степень нагрева элементов свечей зависит от следующих основных факторов:
- Внутренние факторы:
- конструкция электродов и изолятора (длинный электрод и изолятор нагреваются быстрее);
- материал электродов и изолятора;
- толщина материалов;
- степень теплового контакта элементов свечи с корпусом;
- наличие медного сердечника в центральном электроде.
- Внешние факторы
- степень сжатия и компрессии;
- тип топлива (более высокооктановое обладает большей температурой сгорания);
- стиль езды (на больших оборотах и нагрузках двигателя нагрев свечей больше);
- состав смеси (на бедных нагрев выше) и угол опережения зажигания.
«Горячие» свечи — конструкция свечей специально разработана таким образом, что снижается теплопередача от центрального электрода и изолятора. Применяются в двигателях с низкой степенью сжатия и при использовании низкооктанового топлива. Так как в этих случаях меньше температура в камере сгорания.
«Холодные» свечи — конструкция свечей специально разработана таким образом, что максимально повышается теплопередача от центрального электрода и изолятора. Применяются в двигателях с высокой степенью сжатия, с высокой компрессией и при использовании высокооктанового топлива, а также в двигателях с воздушным охлаждением, отличающихся повышенной тепловой напряжённостью камеры сгорания.
«Средние» свечи — занимают промежуточное положение между горячими и холодными (самые распространенные)
Типовые размеры и маркировка свечей зажигания
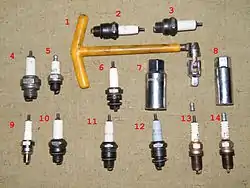
2 — А14В, резьба М14×1,25×12, ключ 21;
3 — А11Н, резьба М14×1,25×11, ключ 22;
4 — М8, резьба М18×1,5×12, ключ 24;
5 — для бензопил, резьба М14×1,25×11, ключ 19;
6 — СИ12РТ (для лодочных моторов), резьба М14×1,25×12, ключ 21;
7 — торцовая головка на 21 мм
8 — торцовая головка на 16 мм;
9 — резьба М10×1×12, ключ 16;
10 — А10Н, резьба М14×1,25×11, ключ 22;
11 — А11-3, резьба М14×1,25×12, ключ 21;
12 — А17В, резьба М14×1,25×12, ключ 21;
13 и 14 — резьба М14×1,25×19, ключ 16, контактная гайка съёмная.
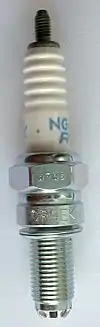
Размеры свечей зажигания классифицируются по диаметру резьбы на них. Применяются следующие типы резьбы:
- M10×1 (мотоциклы, например, свечи типа «Т» — ТУ 23; бензопилы, газонокосилки);
- M12×1,25 (мотоциклы);
- M14×1,25 (автомобили, все свечи типа «А»);
- M18×1,5 (свечи типа «М», старый американский стандарт; устанавливались на старые автомобильные двигатели М-20, ГАЗ-51, ГАЗ-69; «тракторные» свечи; свечи для газопоршневых ДВС и др.)
Вторым классификационным признаком служит длина резьбы:
- короткая — 12 мм (ЗИЛ, ГАЗ, ПАЗ, УАЗ, Волга, Запорожец, мотоциклы);
- длинная — 19 мм (ВАЗ, АЗЛК, ИЖ, Москвич, Газель, практически все иномарки);
- удлинённая — 26,5 мм (современные форсированные ДВС);
- на малогабаритные двигатели могут устанавливаться свечи с более короткой резьбой (меньше 12 мм)
Размер головки под ключ (шестигранник):
- 24 мм (свечи марки «М8» с резьбой M18×1,5)
- 22 мм (свечи марки «А10» «А11», двигатели автомобилей ЗИС-150, ЗИЛ-164; все свечи по старому ГОСТ 2043-54)
- 20,8 мм (в обиходе часто округляют до 21 мм; европейский стандарт времён покупки лицензии на выпуск «Жигулей», до сих пор широко применяется для ДВС с двумя клапанами на цилиндр);
- 19 мм (для ДВС некоторых мотоциклов)
- 16 мм или 14 мм (современная, для ДВС с тремя или четырьмя клапанами на цилиндр);
Калильное число (тепловая характеристика):
- «Горячие» свечи: 8…14 единиц по ГОСТ 2043-74 (нижнеклапанные и малофорсированные нижневальные двигатели);
- Свечи со средними характеристиками: 17…19 (форсированные нижневальные двигатели и верхневальные средней степени форсирования);
- «Холодные» свечи: 20 и более (высокофорсированные 4-тактные двигатели, двигатели с воздушным охлаждением, 2-тактные двигатели);
Ранее, по ГОСТ 2043-54, указывалась непосредственно длина теплового конуса свечи в миллиметрах; так, свеча А7,5БС имела длину теплового конуса изолятора 7,5 мм (современный аналог — А17В).
Для иностранных свечей используются свои шкалы тепловой характеристики.
Способ уплотнения по резьбе:
- С плоской прокладкой (с кольцом)
- С конусным уплотнением (без кольца)
Количество и вид боковых электродов:
- Одноэлектродные — традиционные;
- Многоэлектродные — несколько боковых электродов;
- Специальные, более стойкие электроды для работы на газе или для большего пробега;
- Факельные — унифицированные свечи зажигания, присутствует конусный резонатор, для симметричного поджига топливной смеси.
- Плазменно-форкамерные — боковой электрод выполнен в виде сопла Лаваля. Совместно с корпусом свечи образует внутреннюю форкамеру. По заявлениям производителей (Украина), зажигание происходит «форкамерно-факельным способом».
Неисправности свечей зажигания
Свеча может выходить из строя следующими способами:
- загрязнение теплового конуса углеродом и маслом во время длительного безуспешного пуска или езды на непрогретом моторе - приводит к отказу обслуживаемого свечой цилиндра;
- закоксовывание пространства между тепловым конусом и корпусом продуктами сгорания масла, при его большом расходе;
- износ (выгорание) электродов, приводящие к увеличению зазора, что может привести к пробою провода, свечного наконечника, катушки, либо вызывать пропуск зажигания при резком открытии дросселя ("провал газа"). В "платиновых" - полное израсходование напыления, быстрый рост зазора;
- оплавление электродов, растрескивание или разрушение теплового конуса;
- пропуск газов через уплотнение корпуса, приводящее к сильному загрязнению изолятора снаружи, и возможному пробою свечного наконечника.
См. также
Примечания
- Сельскохозяйственный словарь-справочник. — Москва - Ленинград : Государственное издательство колхозной и совхозной литературы «Сельхозгиз». Главный редактор: А. И. Гайстер. 1934 год.
- Двигатель НК-8-2У. Руководство по технической эксплуатации. Часть третья. Глава 80 — «Система запуска»
- Двигатель ПС-90А. Руководство по технической эксплуатации. Книга 3. Раздел 080.00.00 — Система запуска
- Хиллиард Д., Спрингер Дж. Топливная экономичность автомобилей с бензиновыми двигателями. — 1988. — Москва: Машиностроение.