Лазерная наплавка
Ла́зерная напла́вка — метод нанесения материала при помощи лазерного луча, использующегося для создания ванны расплава, куда подается материал. В качестве присадки могут использоваться как порошки, так и проволоки[1].
Технология
Современное оборудование для лазерной наплавки, в основном, оснащается диодными или оптоволоконными лазерными источниками. Помимо этого существуют газовые и другие источники, также используемые для наплавки. Диодные лазеры более всего подходят к процессу наплавки, так как плотность распределения энергии в фокусной точке наиболее равномерна[2].
Лазерная наплавка по характеру излучения бывает:
- Непрерывным лазером
- Импульсным лазером
Существует проволочная и порошковая лазерная наплавка. Лазерное сканирование поверхности с преднанесенным покрытием называется лазерным оплавлением.
Существуют следующие способы подачи материала:
- Коаксиальная.
- Радиальная.
- Латеральная.
Для лазерной наплавки применимы типы лазеров, генерирующих длину волны в диапазоне 0,9—1,3 мкм, так как в этом диапазоне у большинства чистых металлов и сплавов степень поглощения излучения оптимальна.
- Оптоволоконные
- Диодные лазеры
- Алюмо-иттриевые (YB:YAG)
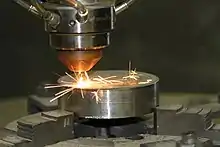
Наплавка непрерывным лазером Непрерывная наплавка характеризуется большей производительностью. Минимальные тепловложения лазерной наплавки перед другими технологиями наплавки и сварки позволяют обрабатывать даже трудносвариваемые материалы. Среднее значение зоны перемешивания материала наплавки с основой составляет 10—30 мкм, в зависимости от режимов наплавки. Толщина наплавки за один проход варьируется от 0,05—3 мм.
Сегодня существуют оптические системы, позволяющие наплавлять как внешние, так и внутренние поверхности. Принципиальным отличием систем для внутренней наплавки является наличие призмы или зеркал поворачивающих поток световой энергии.
Основными потребителями технологий лазерной наплавки являются: нефтегазовая отрасль, металлургия, судостроение, гипсоцементной промышленности.
Наплавка импульсным лазером
Импульсный лазер отличается большой пиковой мощностью, работа по наплавке идёт вручную, в основном проволокой, или с помощью роботизированных систем (проволочная или порошковая). Материал подается в ванну расплава.
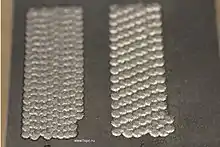
При ручной наплавке наблюдая процесс под микроскопом с увеличением 10—16 крат. В окуляре микроскопа находится перекрестие, по которому выставлятся лазерный луч, поэтому оператор всегда знает куда попадёт следующий импульс. Используемые диаметры сфокусированного луча лазера варьируется в пределах от 0,2—2,5 мм, в зависимости от диаметра подаваемой присадки (d пятна должен быть в 1,5—2 раза больше диаметра присадки, для перемешивания присадки с наплавляемой поверхностью), что позволяет минимизировать объёмы расплава и соответственно уменьшить тепловложения в обрабатываемый материал. В зону наплавки подаётся инертный газ, предохраняющий ванну расплава от доступа кислорода. Ручная наплавка, в основном, применяется для получения первоначальных размеров изношенных или поврежденных деталей. Чаще всего используется для восстановления повреждённых деталей машин и пресс-форм. Поскольку процесс по сути является сваркой с присадкой наплавка идёт во время сварки некоторых деталей.
Роботизированная импульсная наплавка чаще применяется для новых изделий, так как позволяет снизить трещинообразование наплавляемого слоя, благодаря уменьшению теплового воздействия на деталь.
Преимущества лазерной наплавки
- Дозируемая энергия;
- Возможность локальной обработки поверхности;
- Отсутствие термических поводок, минимизация зоны термического влияния;
- возможность обработки деталей больших габаритов с большим расходом наплавляемого вещества;
- Быстрый нагрев и остывание наплавляемого материала;
- Возможность модификации поверхности;
- Высокая степень адгезии наплавляемого материала при небольшом перемешивании с основой[3].
Применение
Лазерная наплавка получила широкое распространение в промышленности. Наиболее известные применения — это восстановление повреждённых поверхностей различных деталей машин, пресс-форм и фильер. Второе применение — это модификация поверхностности. Присадочные материалы могут отличаться по химическому составу от основы и иметь другие свойства. Таким образом упрочняют износившиеся кромки штампов, наплавляя более твёрдый материал.
Более новое применение это прототипирование деталей. Например, 3D-принтер, печатающий металлическим порошком, по сути сплавляет между собой слои порошка[4].
Примечания
- Шишковский И. Лазерный синтез функционально-градиентных мезоструктур и объемных изделий. — 2018. — ISBN 9785040048083.
- Гусенков А. Методы и средства упрочнения поверхностей деталей машин концентрированными потоками энергии. — Москва: Наука, 1992. — 403 с. — ISBN 9785020068704.
- Академия Наук СССР. Известия Академии наук СССР.: Серия физическая, Том 47. — 1983. — С. 834-1664.
- Всесоюзная академия сельскохозяйственных наук имени В.И. Ленина. Механизация и электрификация сельского хозяйства. — Колос, 1990.