Газонаполнительная станция
Газонаполнительная станция (ГНС) — это база снабжения СУГ, включающая комплекс технологического оборудования, предназначенного для выполнения операций по приему, хранению и наполнению баллонов и цистерн автомобильных газовозов. Кроме того комплектация оборудования ГНС может обеспечивать также диагностику, ремонт и восстановление баллонов. ГНС различаются по производительности и технологической оснащенности согласно основному предназначению. Производительность газонаполнительной станции зависит от потребности в сжиженном газе обслуживаемой ей территориальной зоны. Технологическая оснащенность зависит от производительности и от преимущественного характера выполняемых операций. ГНС, имеющие ёмкость резервуарного парка до нескольких тысяч тонн и производительность от 25 до 100 тыс. т/год, называются кустовыми базами.
ГНС включает в себя следующие основные технологические компоненты:
- сливная эстакада для выгрузки СУГ из вагонов-цистерн с подъездными путями;
- резервуарный парк хранения СУГ (максимально допустимый объём до 8000 тыс. т.);
- насосно-компрессорный и испарительный участки;
- пункт (цех) наполнения баллонов;
- коммуникации жидкой и паровой фаз СУГ.
Газонаполнительные станции располагают вне населенных пунктов на установленных нормативными документами расстояниях от зданий, сооружений и коммуникаций. Также ГНС располагают вблизи нефтеперерабатывающих предприятий для поставки СУГ непосредственно с завода. Территория ГНС в обязательном порядке должна быть огорожена и разделяется на две основные зоны: рабочую, включающую главную эстакаду, хранилище, насосно-компрессорный и испарительный участки, цех наполнения баллонов, колонки для наполнения автоцистерн и вспомогательную, с административно-хозяйственными помещениями, гаражом и резервуаром хранения противопожарного запаса воды.

Технологический процесс функционирования ГНС
СУГ поступает на базу двумя способами: либо по трубопроводу из НПЗ, либо по железной дороге в вагонах-цистернах (в этом случае они опорожняются на специальной сливной эстакаде). Затем он поступает на хранение в резервуарный парк ГНС. Пустые баллоны доставляются в пункт (цех) наполнения. В зависимости от производительности данного участка возможно применение различных средств механизации процесса выгрузки вручную, либо с помощью различного типа конвейеров (дисковых, цепных, роликовых раздвижных, подвесных и т. п.). Кроме того, в последнее время получают широкое распространение, особенно в развитых странах, где имеется стойкая тенденция перехода от дорогого ручного труда к использованию промышленных роботов, паллетные системы выгрузки. Паллетные установки выпускаются в разных вариантах: от систем с ручным (для газонаполнительных станций небольшой производительности) или полуавтоматическим управлением до полностью автоматических. Одним из следствий введения паллетной системы является разделение транспорта на «внешний», доставляющий баллоны от потребителей до ГНС, и «внутренний», перемещающий палеты с баллонами внутри ГНС. При этом водители с «внешнего» транспорта не попадают на внутреннюю территорию.
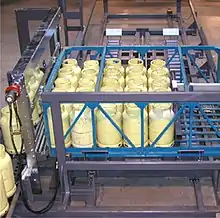
Поскольку баллоны вручную не поднимаются, данная система позволяет минимизировать число производственных травм. Также при транспортировке в палетах баллоны защищены от возможных механических деформаций, что способствует сохранению геометрической формы и окраски. Оснащение пункта (или цеха) наполнения баллонов напрямую зависит от требуемой сменной пропускной способности того или иного типоразмера. Соответственно, они могут оснащаться как компактными наполнительными системами, так и карусельными установками большой производительности. Вообще, существует масса технологических решений по организации процесса заправки газовых баллонов.
Линейная заправочная система с применением ручных или полуавтоматических заправочных постов рассчитана на пропускную способность 50-250 баллонов в час. Конвейерная с применением заправочных каруселей. Такие системы пригодны для заправки любых видов баллонов и могут строиться на базе как цепных, так и роликовых конвейеров.
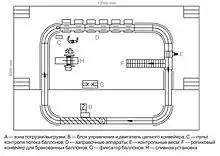
Для учёта отпускаемого газа может использоваться принцип взвешивания или принцип массового расхода. В одну линию заправки могут быть выставлены от 1 до 8 заправочных машин, при проектировании линейных систем можно учесть и заложить в компоновочное решение планируемое в будущем увеличение производительности.
Карусельные заправочные системы производительностью до 1800 баллонов в час являются полуавтоматическими или полностью автоматическими в зависимости от типа применяемого клапана. Уровень автоматизации может быть изменен в зависимости от потребностей.
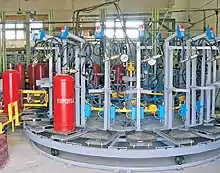
На платформе карусели может быть расположено от 8 до 42 заправочных аппаратов в соответствии с требуемой производительностью. Все оборудование в пределах опасной зоны: цепной конвейер, пункты ввода и вывода, заправочные «карусели» и заправочные аппараты, контрольные весы, сортировочный конвейер, детектор утечек; интерфейс данных и питания изготавливается во взрывозащищенном исполнении. Оборудование в неопасной зоне ограничено компьютером с модемом и принтером и может быть размещено в любом удобном месте за пределами опасной зоны.
Основой всех выше приведенных систем является заправочная машина, предназначенная для безопасной и эффективной заправки всех типов баллонов (различного диаметра, высоты, как с клапанами типа КБ-2, так и с вентилями типа ВБ-2). Для контроля расхода продукта может применяться принцип взвешивания (электронные весы) или принцип массового расхода. При взвешивании необходимо иметь данные пустого баллона для определения точной дозы наполнения СУГ согласно установленной регламентом норме.
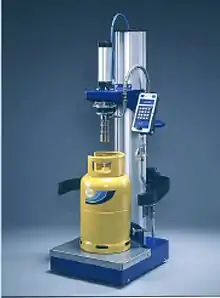
Системы контрольного взвешивания также выпускаются с ручным, полуавтоматическим или полностью автоматическим управлением. Возможны следующие исполнения систем:
- на линии в цепном конвейере с подъемным столом для стационарного контрольного взвешивания или с динамическим столом для непрерывного контрольного взвешивания;
- на линии в цепном конвейере для полностью автоматического контрольного взвешивания с автоматической
передачей веса тары с центральной станции кодирования (при её наличии на ГНС);
- на линии в цепном конвейере для полуавтоматического контрольного взвешивания с ручным кодированием
веса тары;
- на линии в цепном конвейере для полуавтоматического контрольного взвешивания со сверкой тары, которая
осуществляется оператором;
- стационарные контрольные весы для установки на полу.
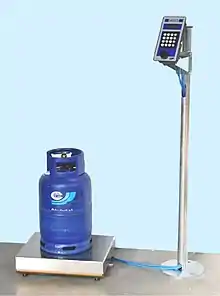
Вспомогательное оборудование ГНС
К вспомогательному оборудованию, используемому при наполнении баллонов относятся различные устройства, как задействованные непосредственно в процессе наполнения, так и в процессе подготовки к нему. К таким устройствам можно отнести:
- машины для проверки ориентации вентиля для выполнения вспомогательной функции в соединении с ручной или автоматической заправкой баллонов с вентилями типа ВБ-2;
- машины для открывания и закрывания баллонов с вентилями типа ВБ-2 для замены ручного труда, автоматизации и ускорения производственного процесса;
- системы слива, используемые для слива конденсата и опустошения баллонов перед их ремонтом, а также для слива переполненных баллонов;
- аппараты для дозаполнения/слива излишков», предназначенных для корректировки веса продукта в заполненном баллоне и приведения веса СУГ к норме в некорректно заполненных баллонах;
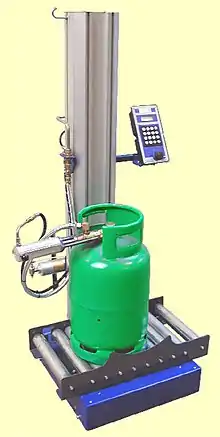
- электронные и ручные детекторы утечек газа для обнаружения утечек паровой фазы СУГ из-под вентиля баллона, а также на седле клапана, в ручном или полностью автоматическом режиме, а также ванны для контроля утечек;
- машины для замены вентилей, используемые при ремонте баллонов;
- системы продувки баллонов, применяемые для быстрого и безопасного вытеснения атмосферного воздуха паровой фазой СУГ;
- оборудование для внутренней очистки и осмотра баллонов СУГ, необходимое при проведении переосвидетельствования баллонов;
- оборудование для проверки баллонов давлением с максимальной производительностью до 450 баллонов в час и испытательным давлением до 4,5 МПа;
- моющие системы для очистки баллонов от всех видов грязи и смазочных веществ;
- машины для выпрямления поверхностей ручек и колец основания баллонов
- оборудование для обработки поверхности баллонов, включающее в себя различные механизмы и устройства для очистки и покраски;
- машины для подготовки списанных баллонов к утилизации, приводящие списанные баллоны в состояние, непригодное для дальнейшей несанкционированной эксплуатации;
- оборудование для маркировки баллонов;
- системы установки термоусадочных колпачков
- системы управления данными, предназначенные для сбора, обработки и передачи данных с работающих заправочных и других технологических аппаратов
Примечания
- Установка вентиля ВБ-2 на баллонах стальных сварных для СУГ давлением 1,6 МПа регламентируется ГОСТ 21804-94 и ГОСТ15860-84.
Ссылки
- Промышленное газовое оборудование: Справочник, 6-е изд., перераб. и доп./под ред. Е. А. Карякина - Саратов: Газовик, 2013. - С.1121 ISBN 978-5-9758-1209-4
- Оборудование для сжиженных углеводородных газов: Справочник, 1-е изд./ под. ред. Е. А. Карякина - Саратов: газовик, 2015. - С.521 ISBN 978-5-9758-1552-1
- Карякин Е. А. Оборудование для газонаполнительных станций// Газ России.2015. №1. С.68